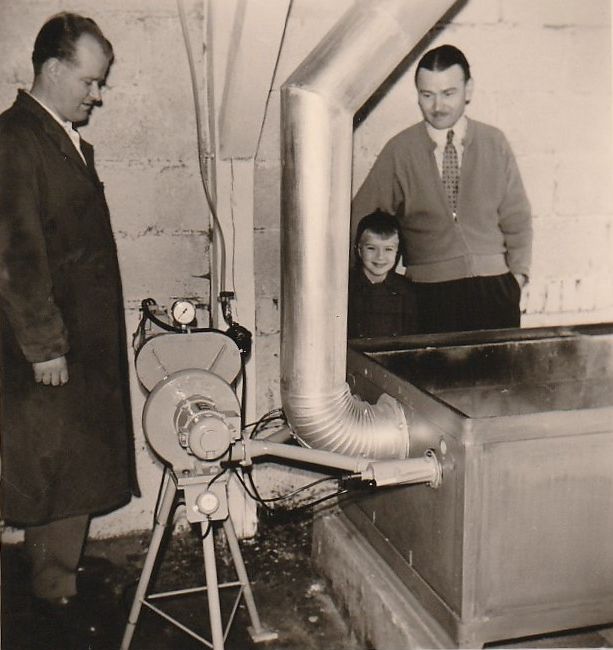 |
Der erste Verzinkungskessel wurde selbst entworfen und gebaut. Planung
und Bau erfolgten durch meinen Vater Helmut (im Bild links) und meinem Großvater Hubert Franke (rechts)
(lngenieur bei Henschel, Kassel) Die Länge betrug ca 0,5 m und wurde
mit einem Ölbrenner beheizt. Ein Kran war nicht vorhanden. Die
Verzlnkung erfolgte per Hand mit einer Zange. Tagsüber bediente mein Vater die
Kunden mit seinem Pkw und einem kleinen Anhänger. Nachmittags und
abends erfolgte die Verzinkung. Die Teile hat er in kleinen
Behältnissen zum Verzinken vorbereitet und gebeizt. Die Anlage befand
sich am hinteren Ende der vorhandenen Halle seines Vaters. Zur
Verzinkung kamen Kleinteile. |
Die erste Anlage in Altmorschen, Elzestrasse, im Bau
|
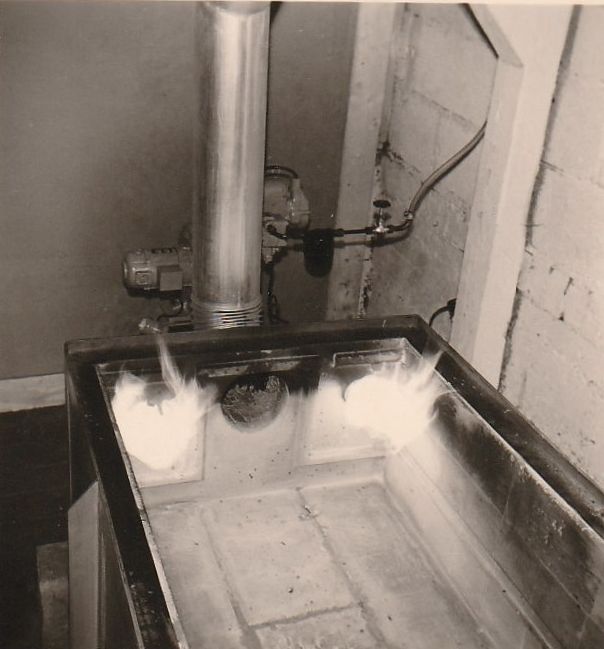 |
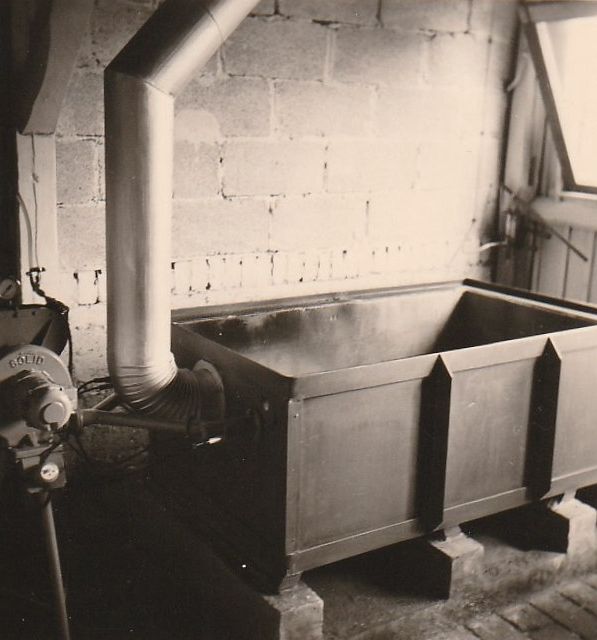 |
Die Geschichte Teil II
Dann kam in den 1960er Jahren der erste Anbau
|
In
den 60er Jahren wurde eine kleine neue Halle quer zur bestehenden Halle
angebaut (Teil II, siehe Foto unten).
Das Bad war größer als das erste (ca. 1-2 m). Auch dieses
wurde selbst entworfen und gebaut. Die Vorbehandlung hat man
entsprechend vergößert. 2-3 Beizbecken in entsprechender Größe. Zur
Arbeitserleichterung stand jetzt auch ein kleiner Schwenkkran zur
Verfügung. Die ersten Mitarbeiter wurden eingestellt, der Onkel von
Helmut, meine Mutter half im Büro. Die Kunden wurden jetzt mit einem
kleinen LKW Marke Borgward, danach mit einem Hanomag bedient. Später
wurde dieser durch einen Mercedes (7,5 t Tragkraft) ersetzt. Zur
Gehäftsfelderweiterung hat man eine Zentrifuge angeschafft, um bei
Kleinteilen (Schüttgut) überschüssiges Zink von den Teilen
abzuschleudern. U.a. wurden Nägel für Holz-Telefonmasten (der EAM) verzinkt.
Desweiteren kam eine kleine Wanne ca. 30 cm lang mit Zinn zum Einsatz.
Hier wurden die Spitzen von Fleischerhaken der Firma Beck und Henkel (Kassel, Schlachthofbau) nach dem verzinken mit einer Zinnschicht
überzogen. Weiter gehörten u.a. größere Firmen in Schlüchtern,
Biedenkopf und Waldkappel zu dem Kundenstamm, die wöchentlich mit dem
LKW besucht und beliefert wurden.
|
Foto aus den 1960/70iger Jahren
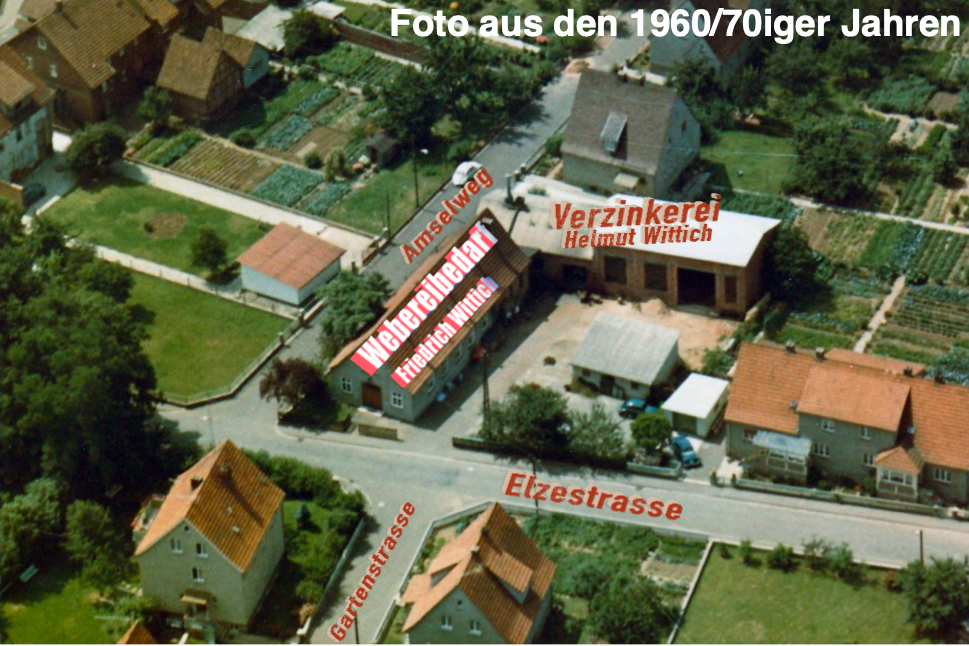 |
Hier begann Teil II
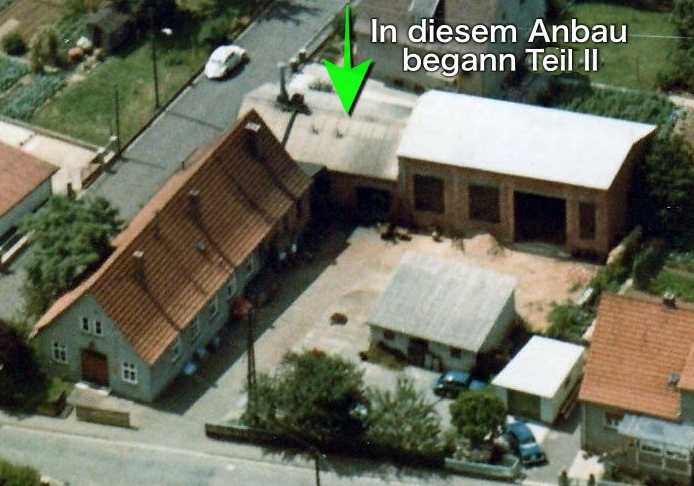 |
Das Zinkbad 2. Greneration war schon größer (2m x 1m)
Hier im Bau. |
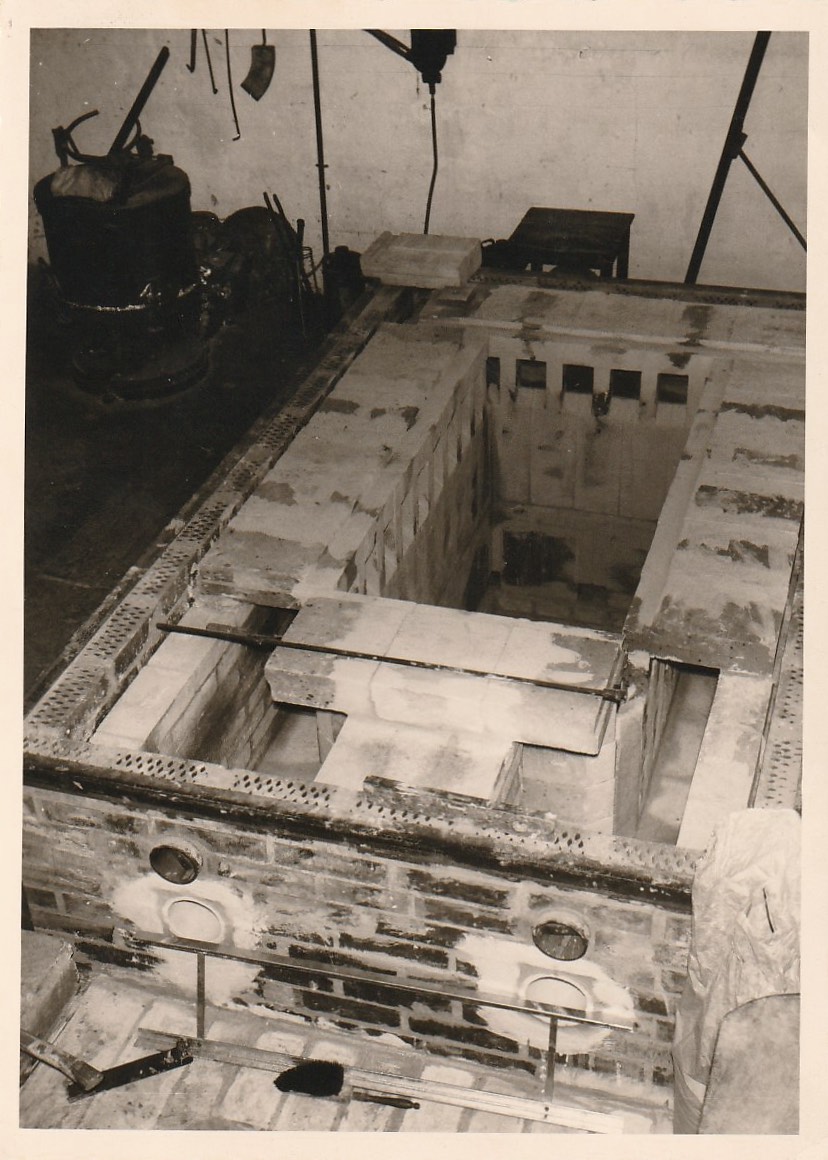 |
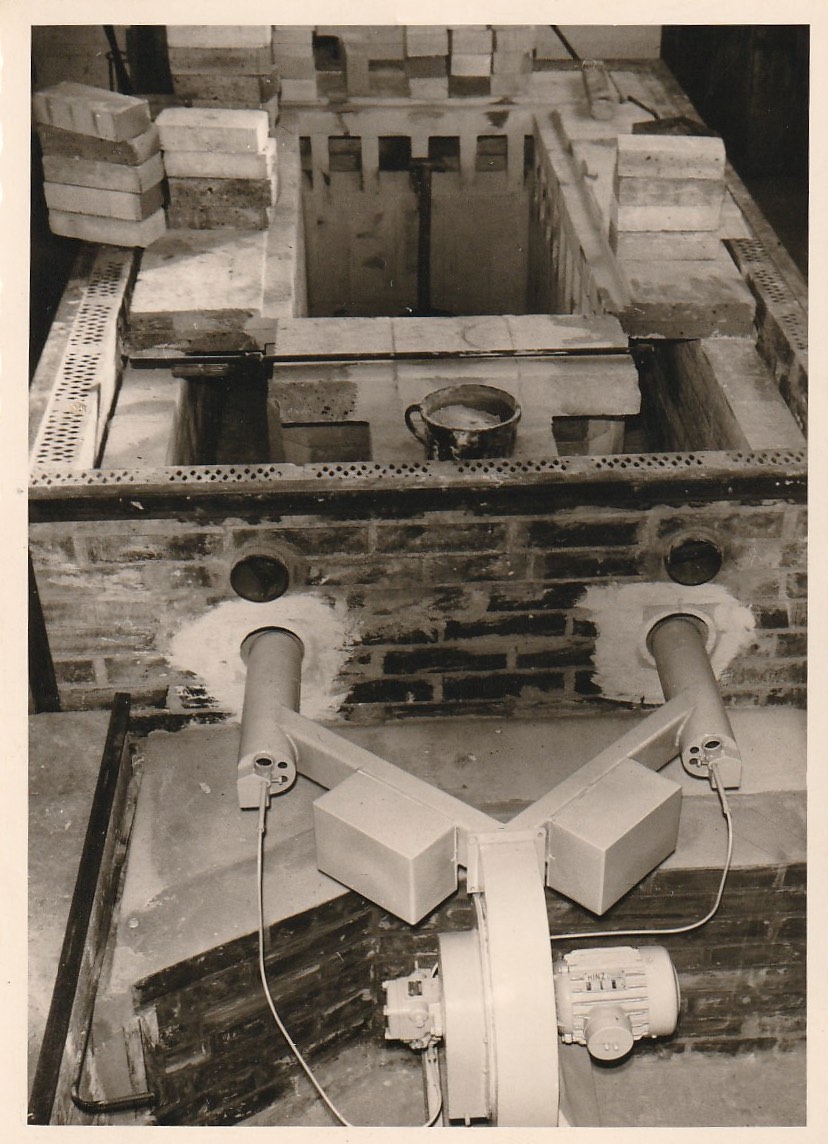 |
Helmut W. verzinkt Teile für die Firma Wiking-Schlauchboote in Hofgeismar
|
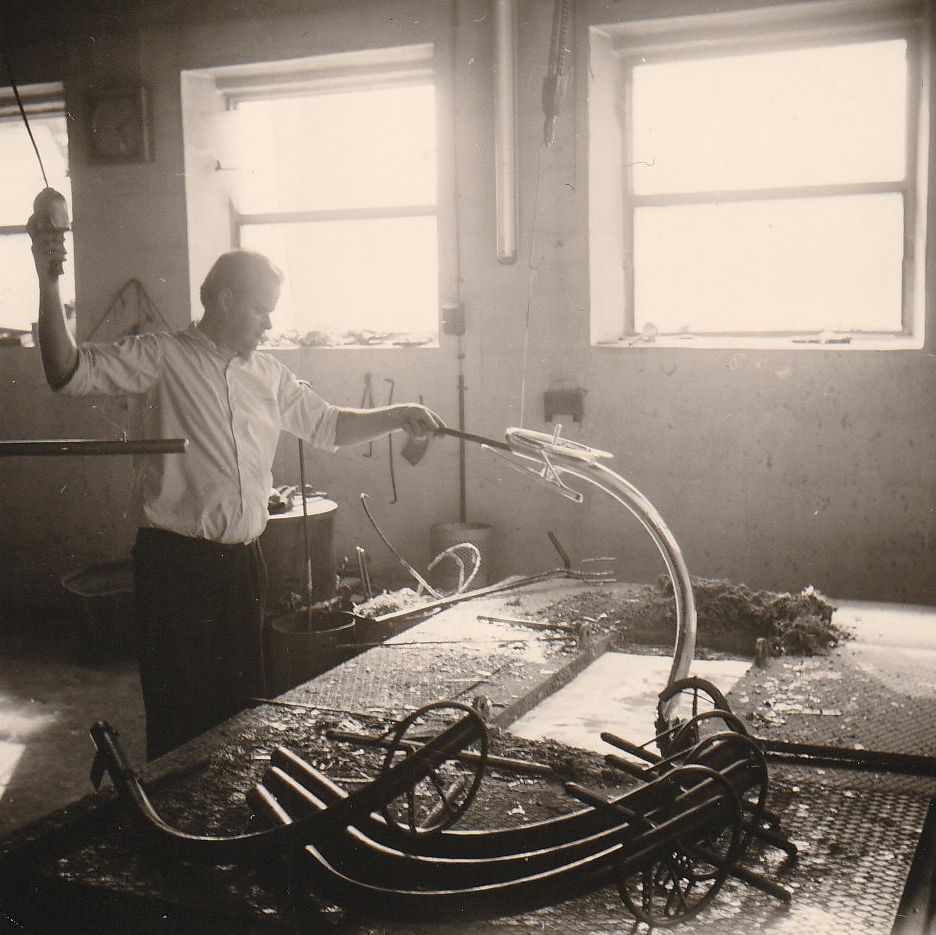 |
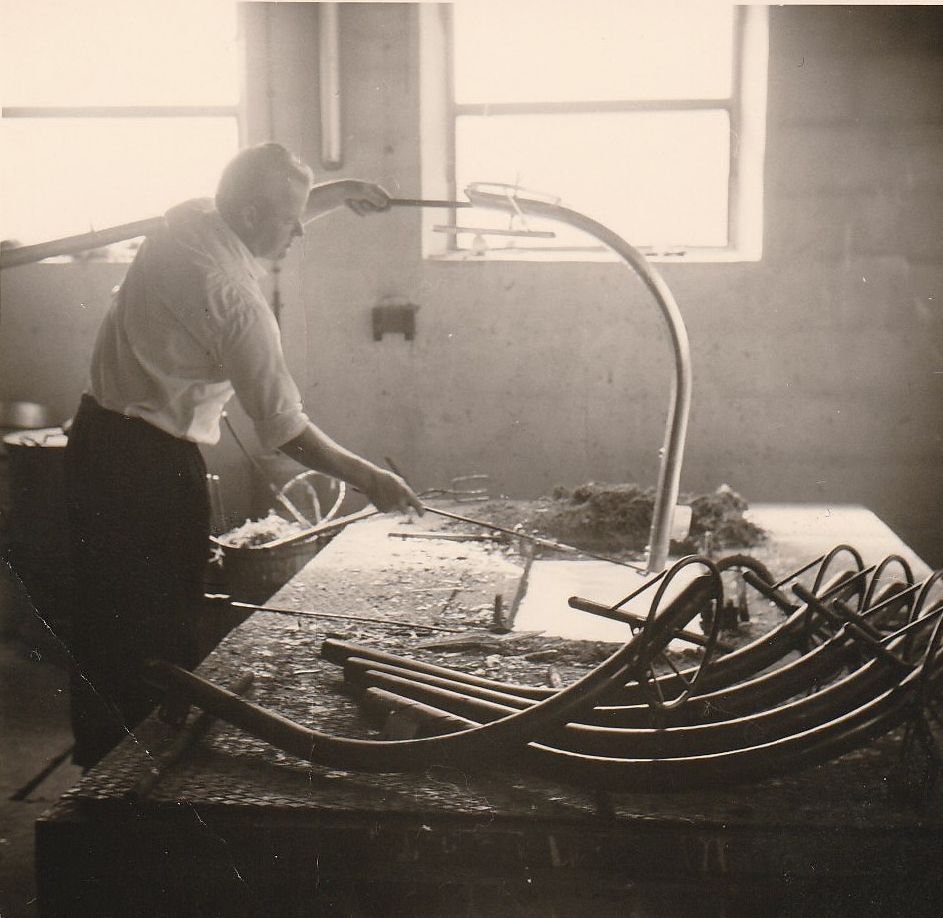 |
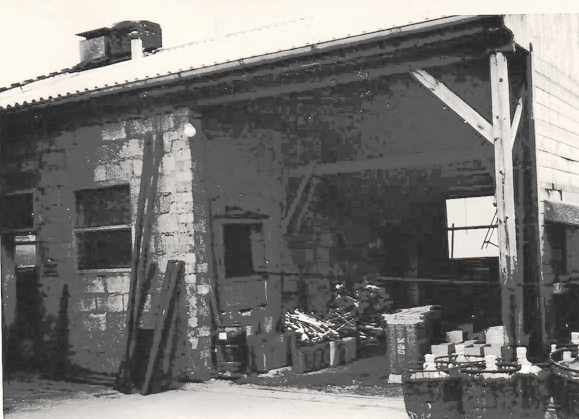
Beizraum (links) und Lagerung verzinkter Teile (rechts |
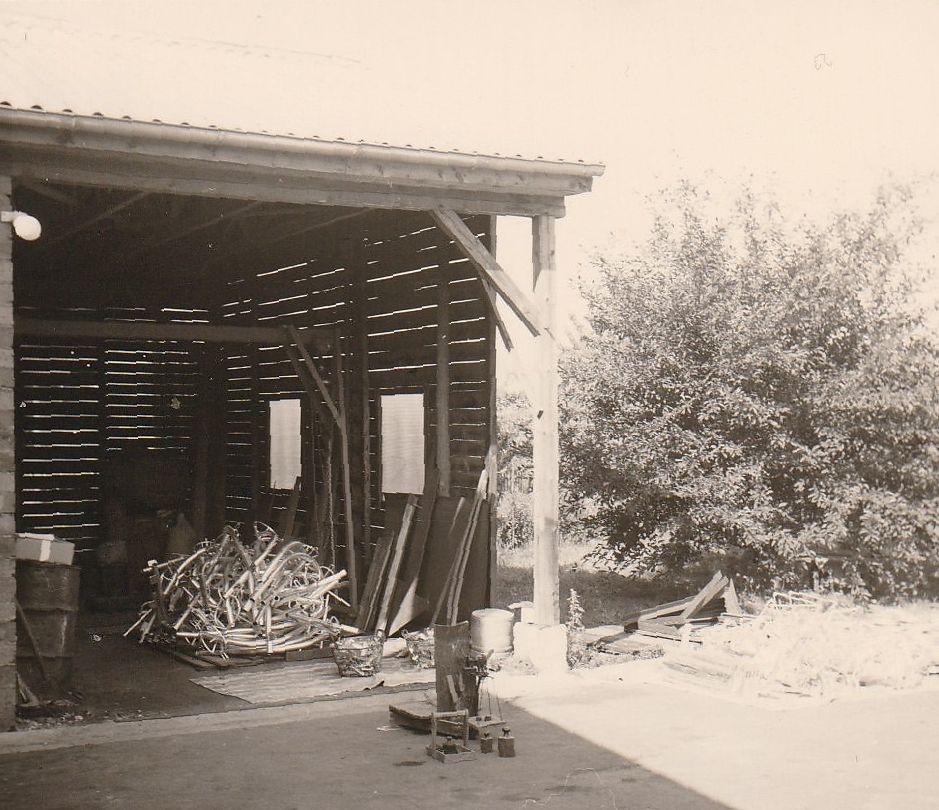 |
|
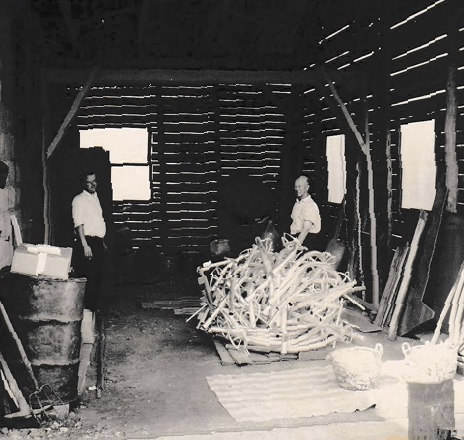 |
Die Geschichte Teil III
Mitte der 1960er Jahre Um-und Anbau
|
Mitte der 60er Jahre ergänzte man die Anlage um drei Bäder die je mit
einer Trommel ausgestattet waren. Hierin wurden Kleinteile u.a.
Befestigungsschrauben für Fahrräder galvanisch verzinkt.
Die Vergrößerung der Halle mit fahrbarer Laufkatze und größerem
Zinkbad (siehe Umbau und Vergrößerung Teil III) stellte dann das Ende
der Entwicklung in Altmorschen dar.
|
Luftaufnahme aus dem Jahr 2017 (Die Verzinkerei exisiert nicht mehr, es stehen nur noch die Gebäude)
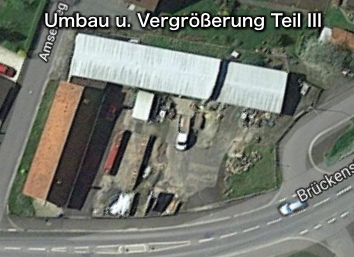 |
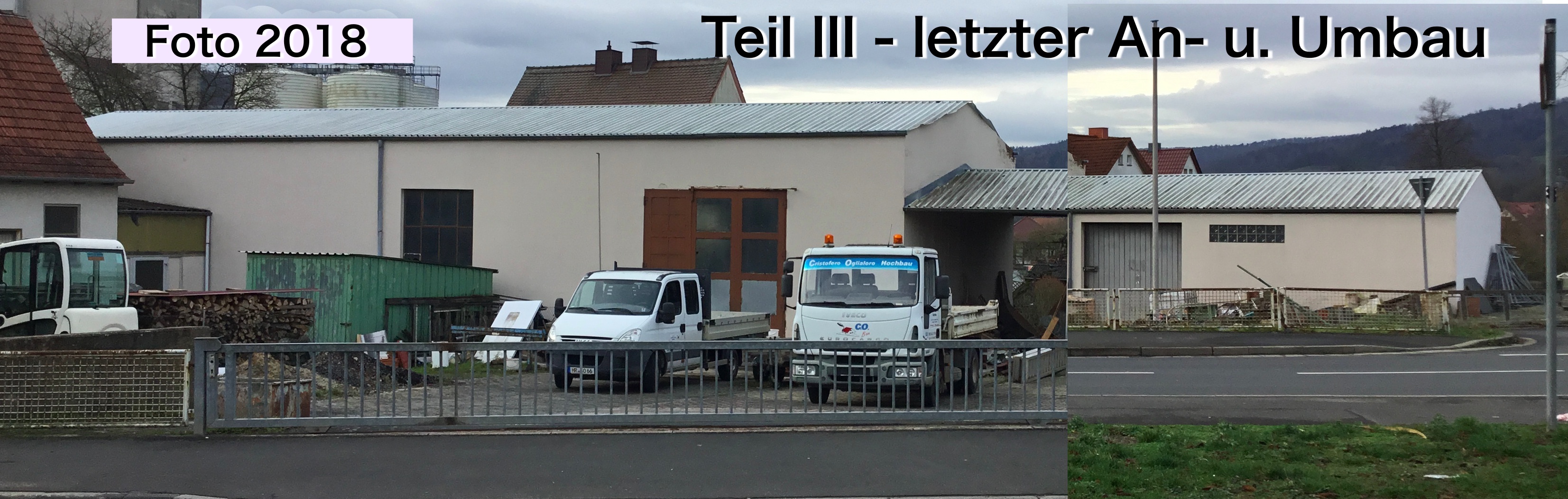
|
Heute (2018) beherbergen die Gebäude ein Bauunternehmen.
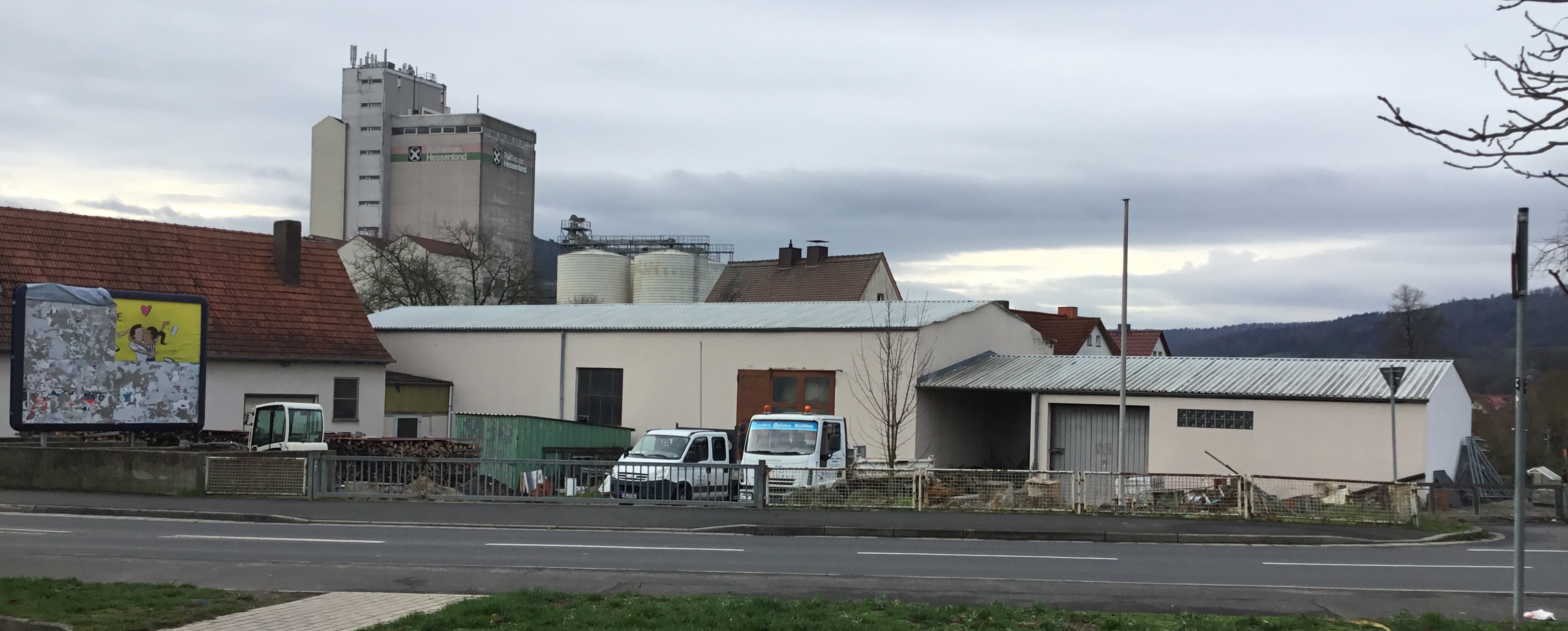
|
|
1971/72 Der Umzug nach Heinebach
|
Ende der 60er
Jahre waren Grundstück und Produktionsstätte zu klein und da man in der
Gemeinde Morschen kein brauchbares Gelände fand, entschloss man sich für
einen Neubau im Industriegebiet in Alheim-Heinebach.
|
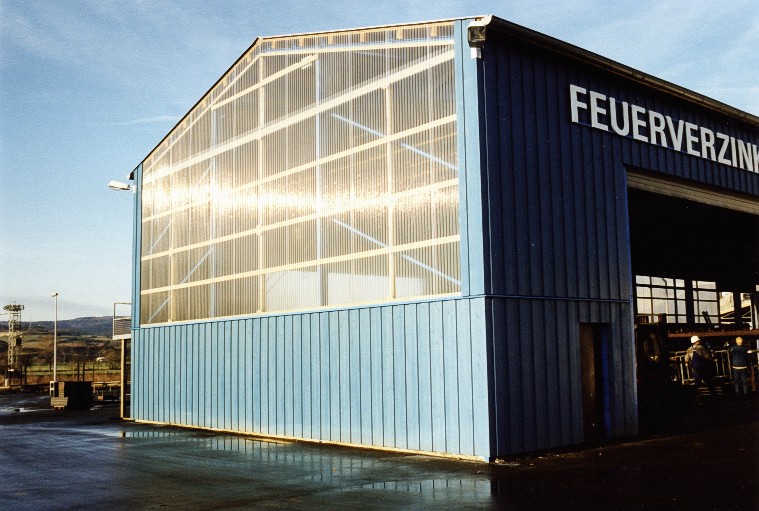
|
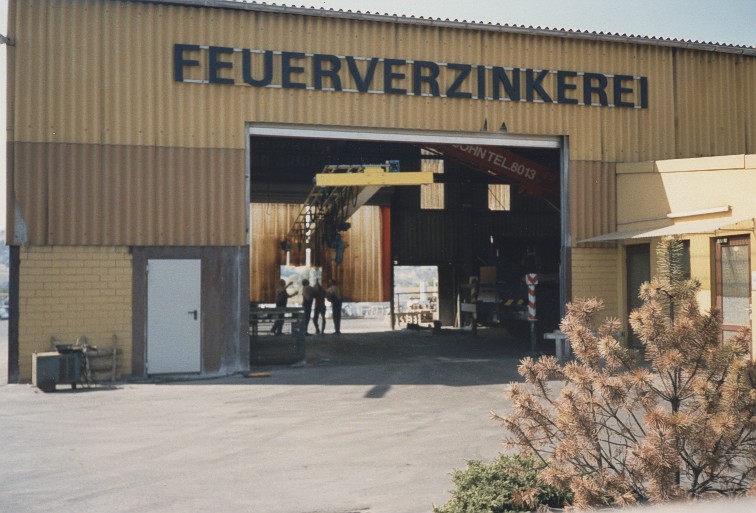
|
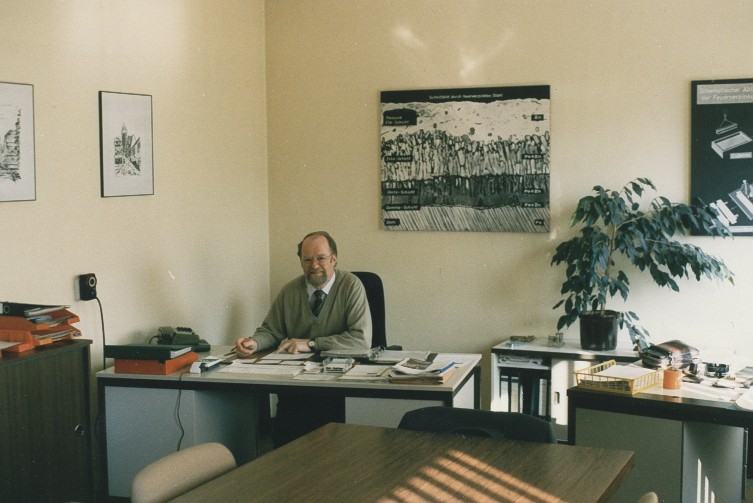
|
|
Der Chef Helmut W. in seinem Büro
|
|
|
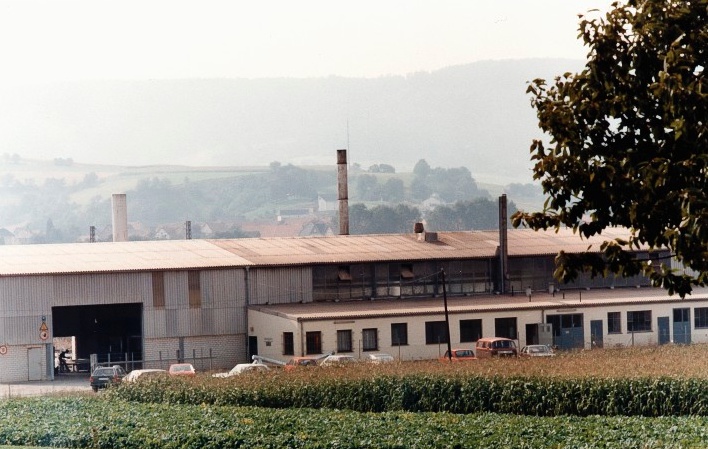
|
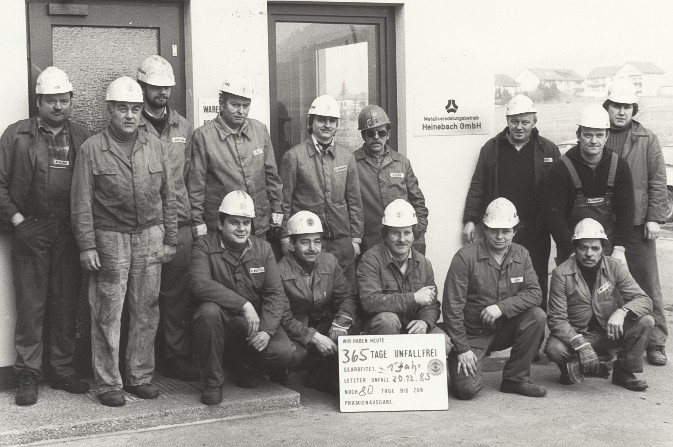 |
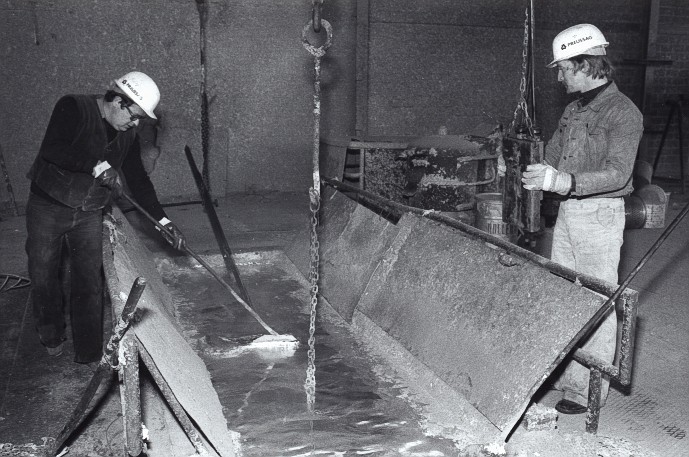
|
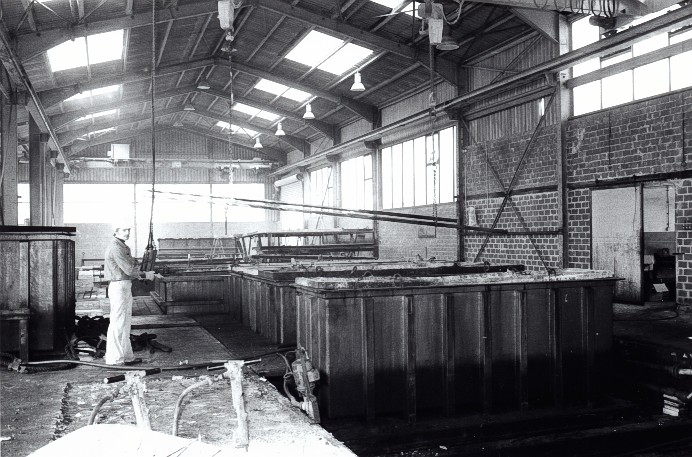
|
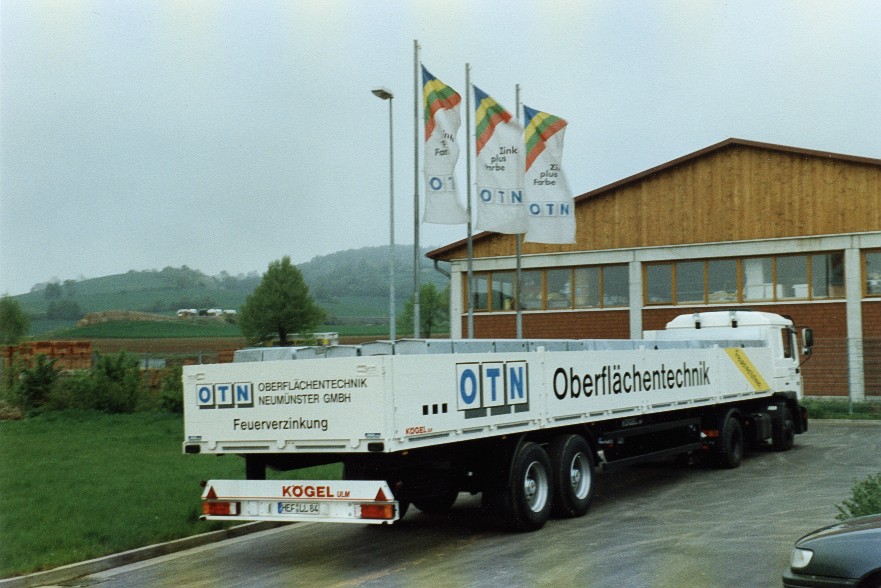 |
|
|
Die
ursprüngliche Hallenlänge betrug ca. 1/3 der aktuellen Hallenlänge (Parallel zur Bahnlänge: blauer Bereich) ohne den abgewinkelten Anbau. Der erste
Verzinkungskessel in Heinebach war ca. 2 - 3m lang.
Daneben war die Zentrifuge untergebracht. Dahinter standen 4
Stahlwannen in denen das Material durch beizen in Salzsäure von Rost
befreit wurde. Voraussetzung für eine einwandfreie Verzinkung ist eine
metallisch reine Oberfläche. Des Weiteren stand ein Brückenkran für den
Materialtransport zur Verfügung. Eine kleine Werkstatt und ein
Bürobereich waren in der Halle integriert. In dem linken Hallenteil
befand sich die Galvanik die von Altmorschen mitgenommen wurde.
Der Hofbereich war unbefestigt. Der Materialtransport und die
Materialverladung erfolgten mittels Gabelstapler.
Ende der 1970er Jahre wurde die Verzinkerei an den Preussag Konzern
verkauft und nannte sich von da an Preussag Metallveredelungsbetrieb
Heinebach GmbH. Später änderte man den Namen in OTN Oberflächentechnik Heinebach.
Die Verzinkerei war jetzt der Oberflächentechnik Neumünster
als Schwesterbetrieb angegliedert. In den Jahren vor und nach dem
Verkauf wurde die Halle verlängert, Büro und Sozialbereich vergrößert.
Verzinkungskessel und Vorbehandlung wurden vergrößert.
Kontinuierlich
ist in diesen Jahren der Kundenstamm, der Fuhrpark und somit das
Personal in Heinebach gewachsen. Innerbetrieblich wurde der Betrieb
ständig an den aktuellen Stand der Technik angepasst. Regelmäßige Instandhaltungsarbeiten stellten den
Produktionsablauf sicher. Den Stahlkessel zur Verzinkung hat man
bedingt durch den Verschleiß regelmäßig gewechselt. Die Anzahl und
Größe der Becken in der Vorbehandlung hat man entsprechend der
Anforderungen angepasst. Da Neumünster über eine Galvanik verfügt wurde diese in
Heinebach abgebaut. Übergroße Teile wurden regelmäßig nach Neumünster
gefahren und dort für Heinebach verzinkt.
Bedingt
durch den ständigen Zuwachs der Kunden musste man das Personal
erweitern. Anfang der 1980 er Jahre waren ca. 15 Mitarbeiter
beschäftigt.
|
1987
hatte man einen Personalstamm von ca. 25 Mitarbeitern in den Bereichen
Produktion, Fuhrpark und Verwaltung. Gearbeitet wurde in 2 Schichten.
Die Kunden wurden mit 3 Lkw bedient. Der Kundenstamm erstreckte sich
entlang der innerdeutschen Grenze von Göttingen über nördlich Kassel
bis Fulda.
Die Verzinkungsanlage hatte eine Größe von 7 m Länge x 1,6 m
Breite x 2,4 m Tiefe. In der Vorbehandlung standen 10 Bäder bis 8 m
Länge zur Verfügung. Bedient wurde die Anlage mit 3 Brückenkränen und
Gabelstapler. Im hinteren Hallenbereich wurden die Teile mit Draht an
Vorrichtungen angebunden in der Mitte vorbehandelt und hinten verzinkt
und abgehängt.
Ende 1980 erhielt der Verzinkungskessel eine
Randabsaugung und eine Filteranlage. Die beim Verzinkungsprozess
entstehenden Emissionen wurden abgesaugt in der Filteranlage gereinigt.
Einbau eines neuen Verzinkungskessels durch das geöffnete Hallendach
|
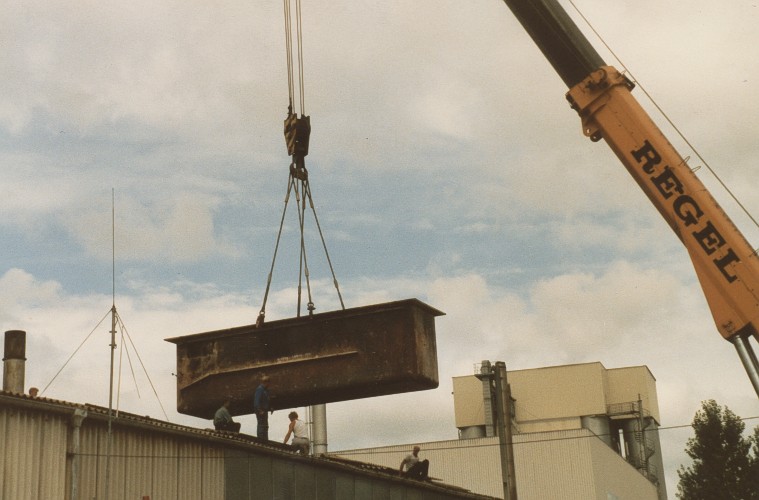
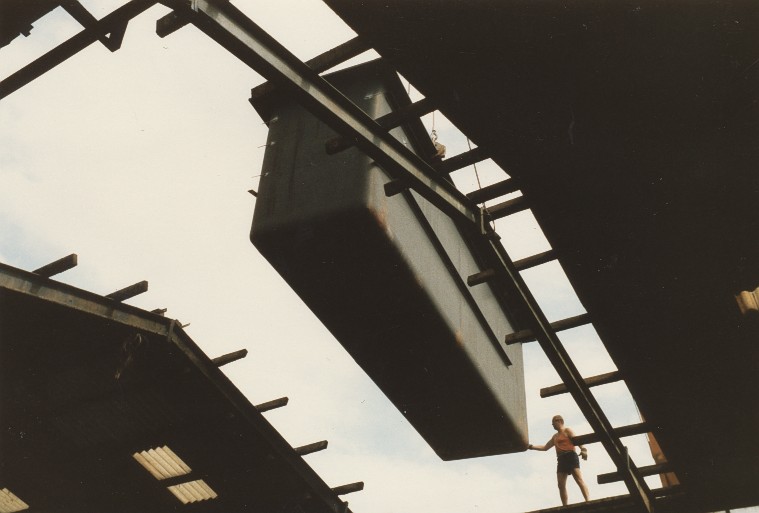
|
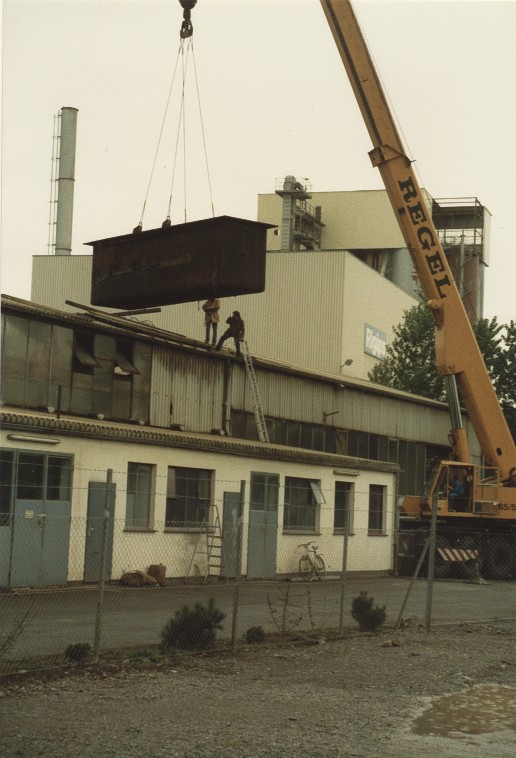
|
|
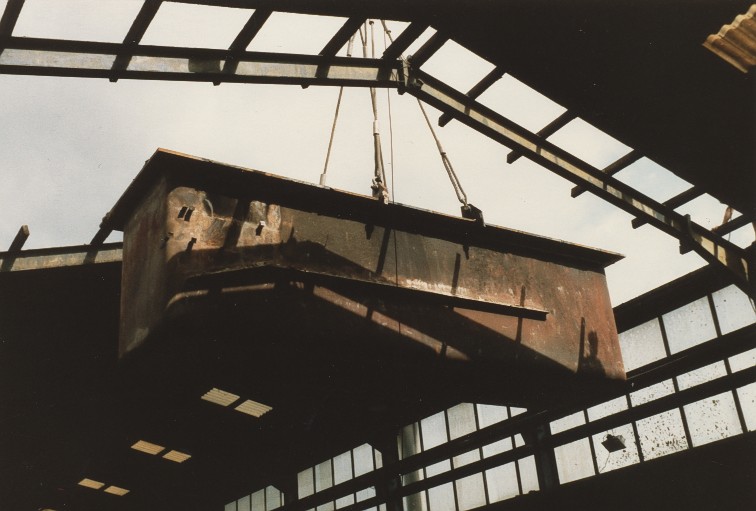 |
|
|
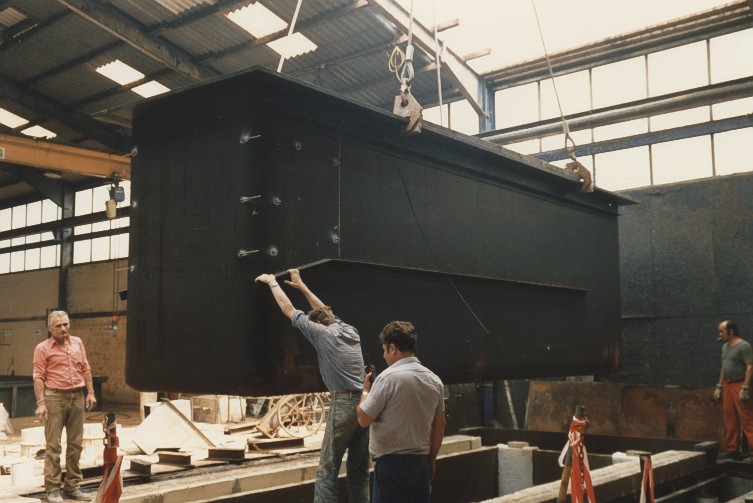 |
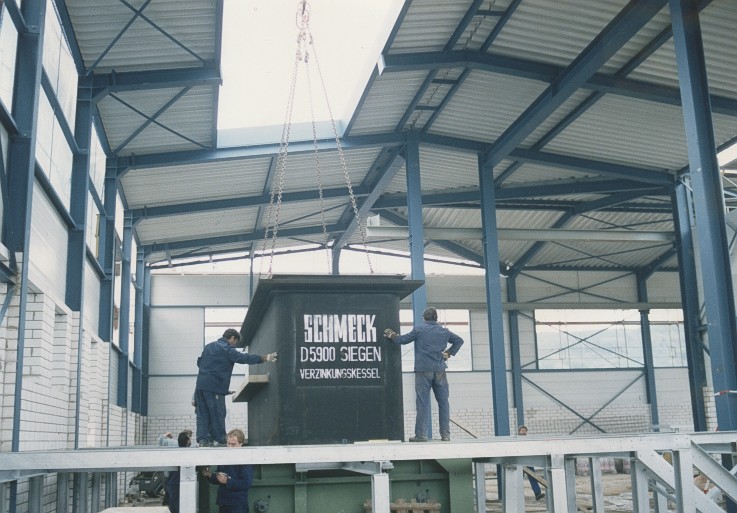 |
Durch den Wegfall der innerdeutschen Grenze 1989 vergrößerte sich das
Einzugsgebiet. Der Bereich Thüringen kam hinzu und somit erhöhte sich
auch das Materialaufkommen. Hierdurch bedingt wurde die Produktion auf
3 Schichten erweitert und das Personal auf ca. 38 Mitarbeiter
erweitert. Die Kunden in den einzelnen Touren fuhr man 2 x pro Woche
mit jetzt 4 Fahrzeugen an. Großteile gingen wöchentlich im Tourendienst
zur Verzinkung nach Neumünster.
Da die Kapazitätsgrenze erreicht war plante man eine Erweiterung der
Anlage.
1992
erfolgte der Anbau einer neuen Halle rechtwinklig an den
alten Hallenteil. In dem neuen Bereich baute man einen Trockenofen ein.
Der Verzinkungskessel sowie der Nacharbeitsbereich mit Materiallager
für die verzinkten Teile kamen in die neue Halle (gelber Bereich).
Der Sozialbereich für
die Mitarbeiter und der Bürobereich wurde vergrößert und modernisiert.
In der alten Halle entfernte man den alten Verzinkungskessel. Die
Vorbehandlung ergänzte man um 3 weitere Becken auf jetzt 13
Vorbehandlungsbäder.
Durch die Optimierung des Produktionsablaufes wurde die Produktion wieder auf 2
Schichten umgestellt und das Personal entsprechend angepasst. Nach und
nach hat man aus Kostengründen den eigenen Fuhrpark ausgelagert. Am
Ende der Umstellung hat eine Spedition mit 3 Lkw mit Anhänger und 1
Sattelzug die Kunden bedient.
|
Werk Heinebach in 1992
|
Bild durch anklicken vergrößern.
|

|
Grundriss des Werkes nach Um- und Anbauten
|
|
Einweihung der neuen Anlage am 13. November 1992
|
|
|
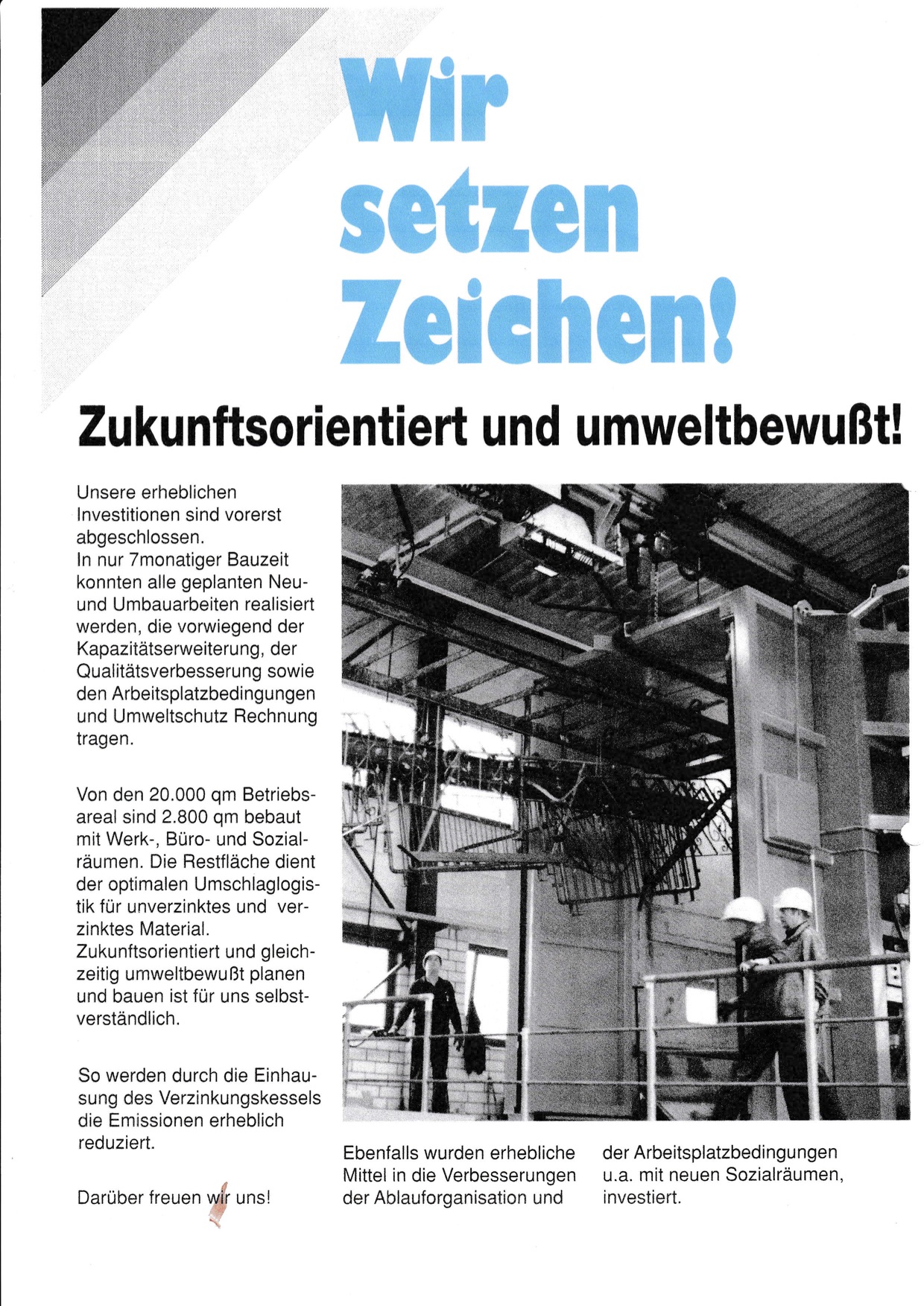 |
Artikel aus der Zeitschrift "Metaleurop"
Ganzer Artikel zweisprachig
französisch - deutsch
(durch anklicken vergrößern)
|
Der deutschsprachige Teil
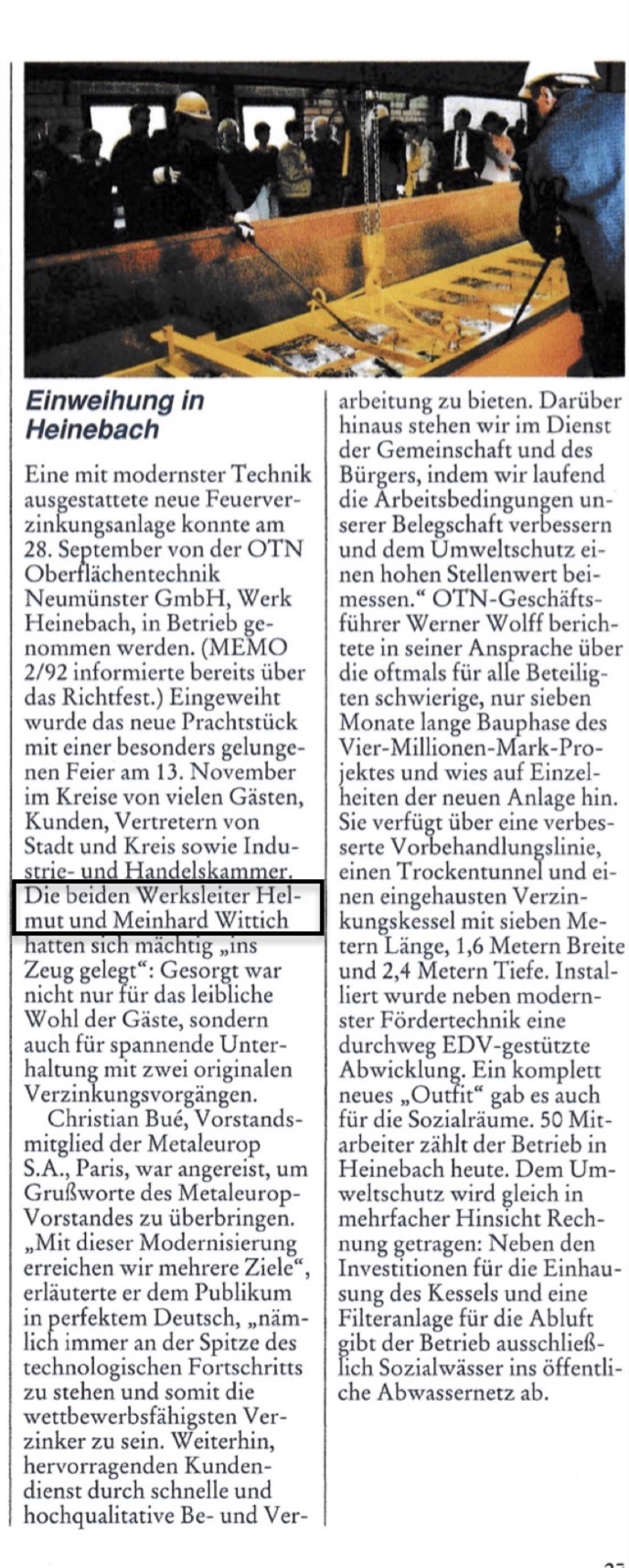 |
|
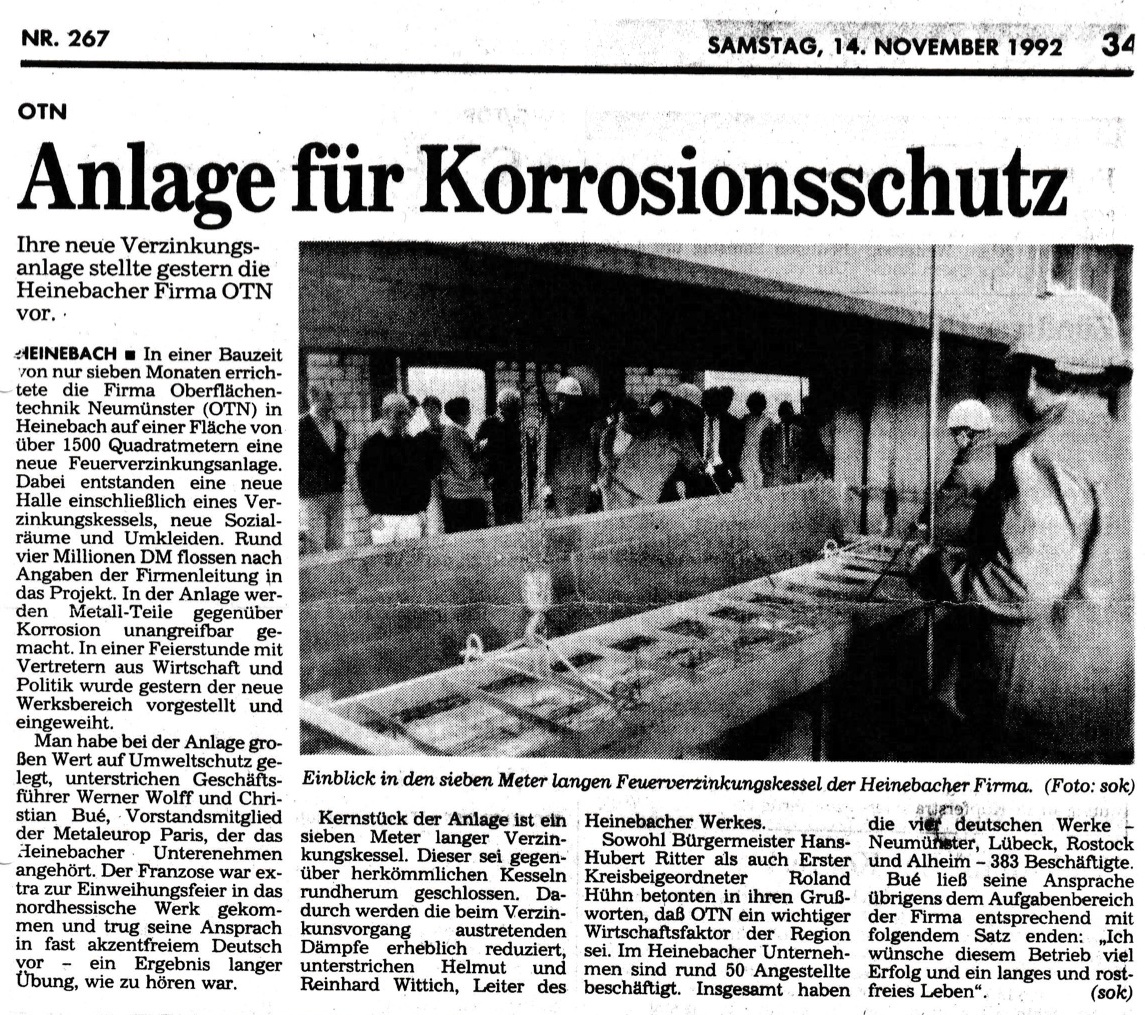
vergrößern: Artikel anklicken!
|
|
|
01.10.1996
Aus logistischen Gründen wurde Heinebach als Schwesterbetrieb von OTN
Neumünster an die OTC Oberflächentechnik Calbe GmbH & Co KG
überstellt. Alle Verwaltungsaufgaben sowie Einkauf wurden von Calbe
aus bearbeitet. Ab da führte man den Namen OTC Feuerverzinkerei
Heinebach. |
|
|
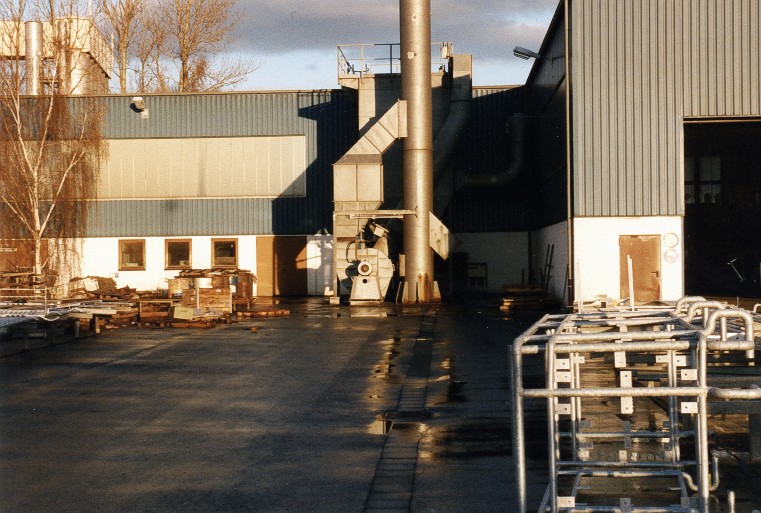 |
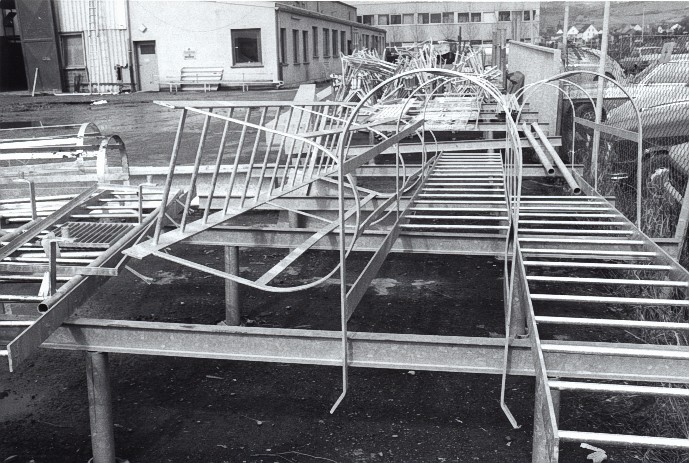 |
|
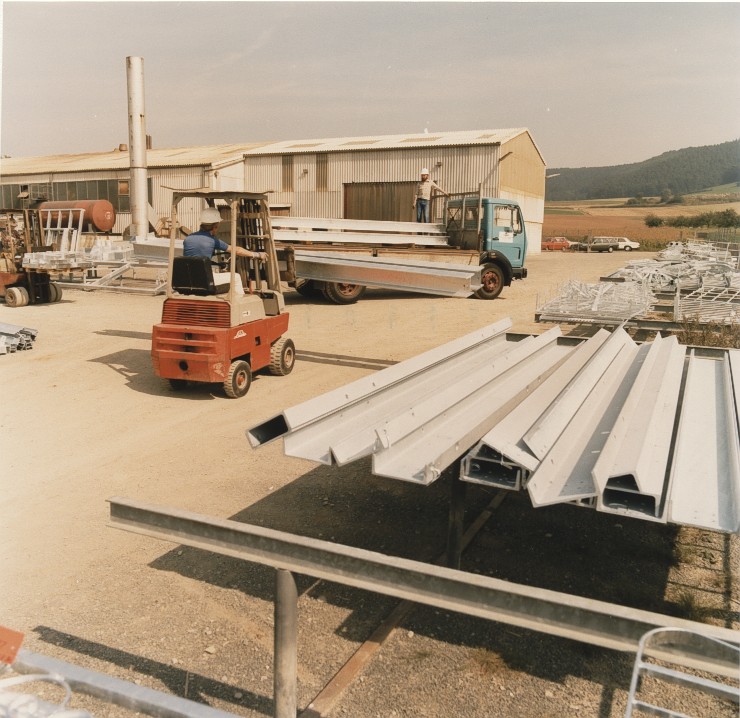 |
|
|
 |
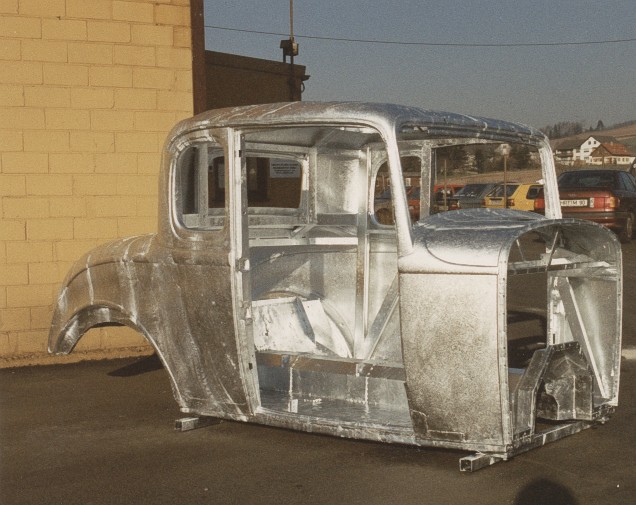 |
|
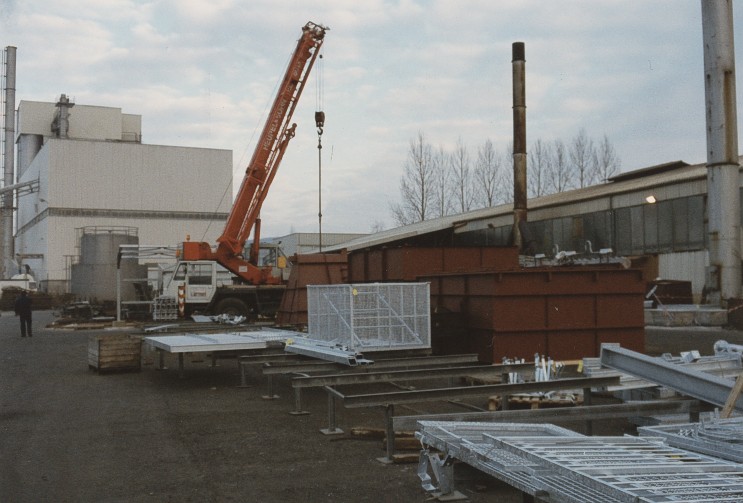 |
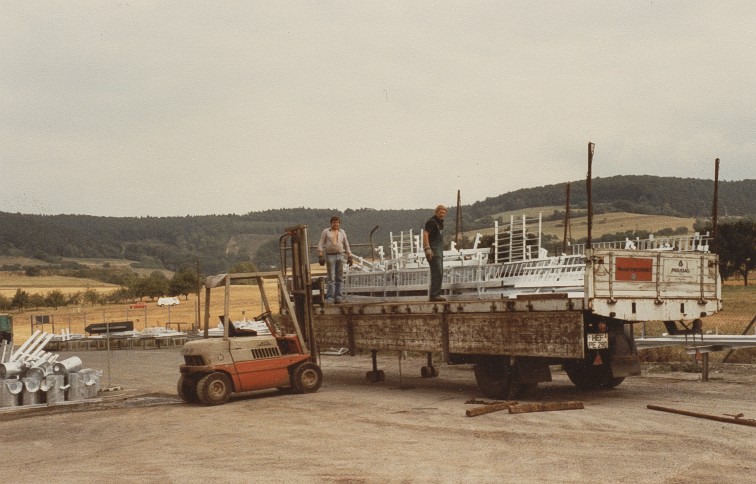 |
|
|
Im Jahr 2000
wurden alle 13 Verzinkereien von der Kopf Gruppe*, u.a. auch Heinebach übernommen.
In diesem Jahrzehnt stand eine weitere große
Instandsetzungsmaßnahme an. Der alte Hallenteil wurde von Grund auf
saniert. Die komplette Wand – und Dachverkleidung entfernte man. Danach
hat man die gesamte Stahlkonstruktion mittels sandstrahlen entrostet und anschließend
vierfach neu beschichtet. Nachdem ein neues Holzdach eingebaut war
erhielt die Halle eine neue Dach und Wandverkleidung. Diese Arbeiten
führte man Tag aus. Die Produktion verlegte man in die Nachtstunden.
Zum Ende des Jahrzehnts hatte man sich der allgemeinen Wirtschaftslage
und dem Wettbewerb angepasst.
Alle Kunden wurden jetzt im Rhythmus von
2 Tagen im Rahmen der Tour mit 4 Fahrzeugen bedient. Der Personalstamm
bestand aus 15 Mitarbeitern. Auftragsspitzen fing man mit dem Einsatz
von Leiharbeitskräften auf. Hierdurch war eine flexible Umstellung von
einer auf zwei Schichten in der Produktion möglich.
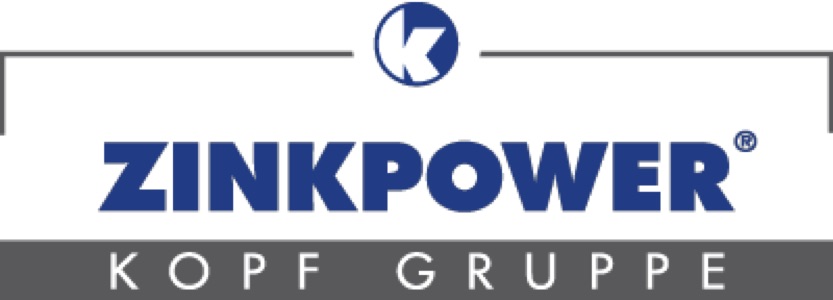 |
*) KOPF GRUPPE (2018)
Die Kopf Gruppe
besteht aus den Geschäftsbereichen ZINKPOWER® und POWER-CAST und
beschäftigt insgesamt über 2.600 Mitarbeiter in 11 Ländern. Sitz der
Kopf Holding GmbH ist Kirchheim/Teck in der Nähe von Stuttgart.
ZINKPOWER
Gehört zu den weltweit
führenden Feuerverzinkungsgruppen. Unter der Marke ZINKPOWER® sind 40
Verzinkereien in 11 Ländern Europas, Amerikas und Asiens vertreten.
Im Jahr 2000 Übernahme von 13
deutschen Verzinkereien und einem Druckgussbetrieb von der Metaleurop
Weiterverarbeitung GmbH - die größte Akquisition in der Geschichte der
Kopf Gruppe. |
|
|
26. September 2008 - 50 Jahre Verzinkerei
|
Bilder von der Jubiläumsfeier
|
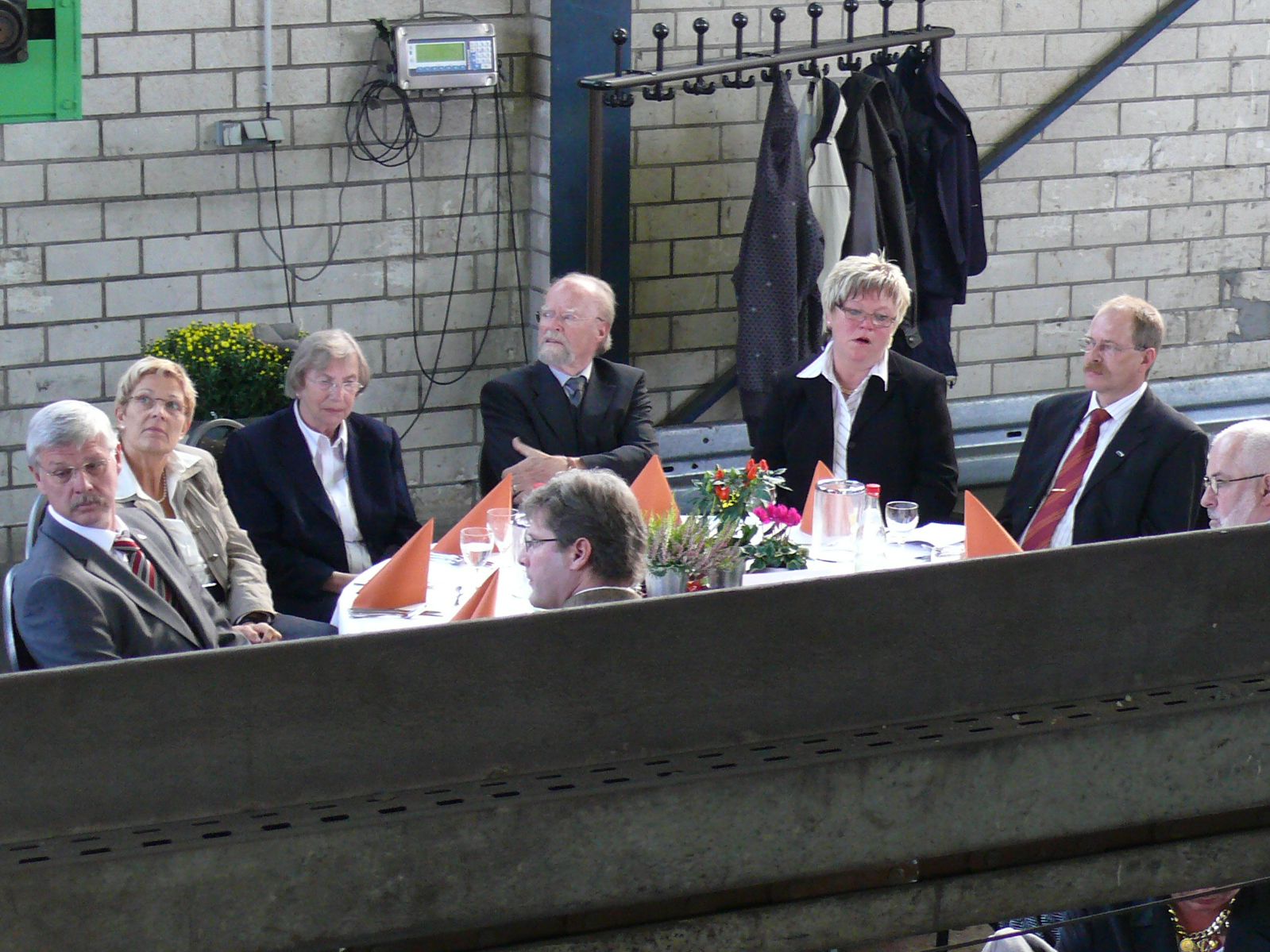
|
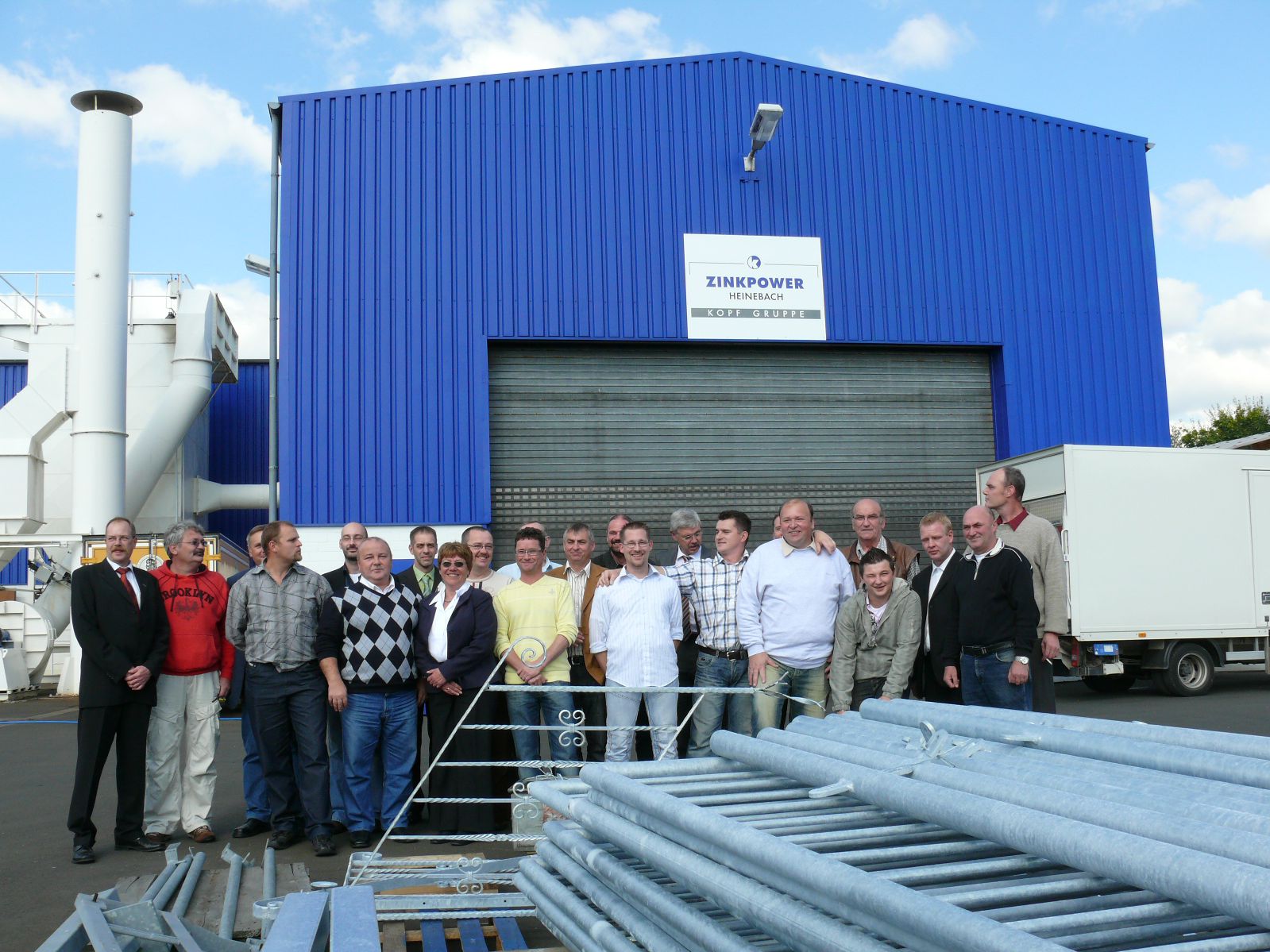
|
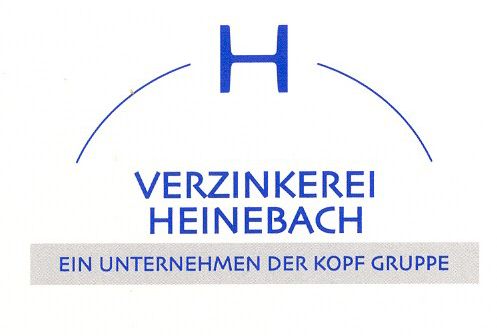
|
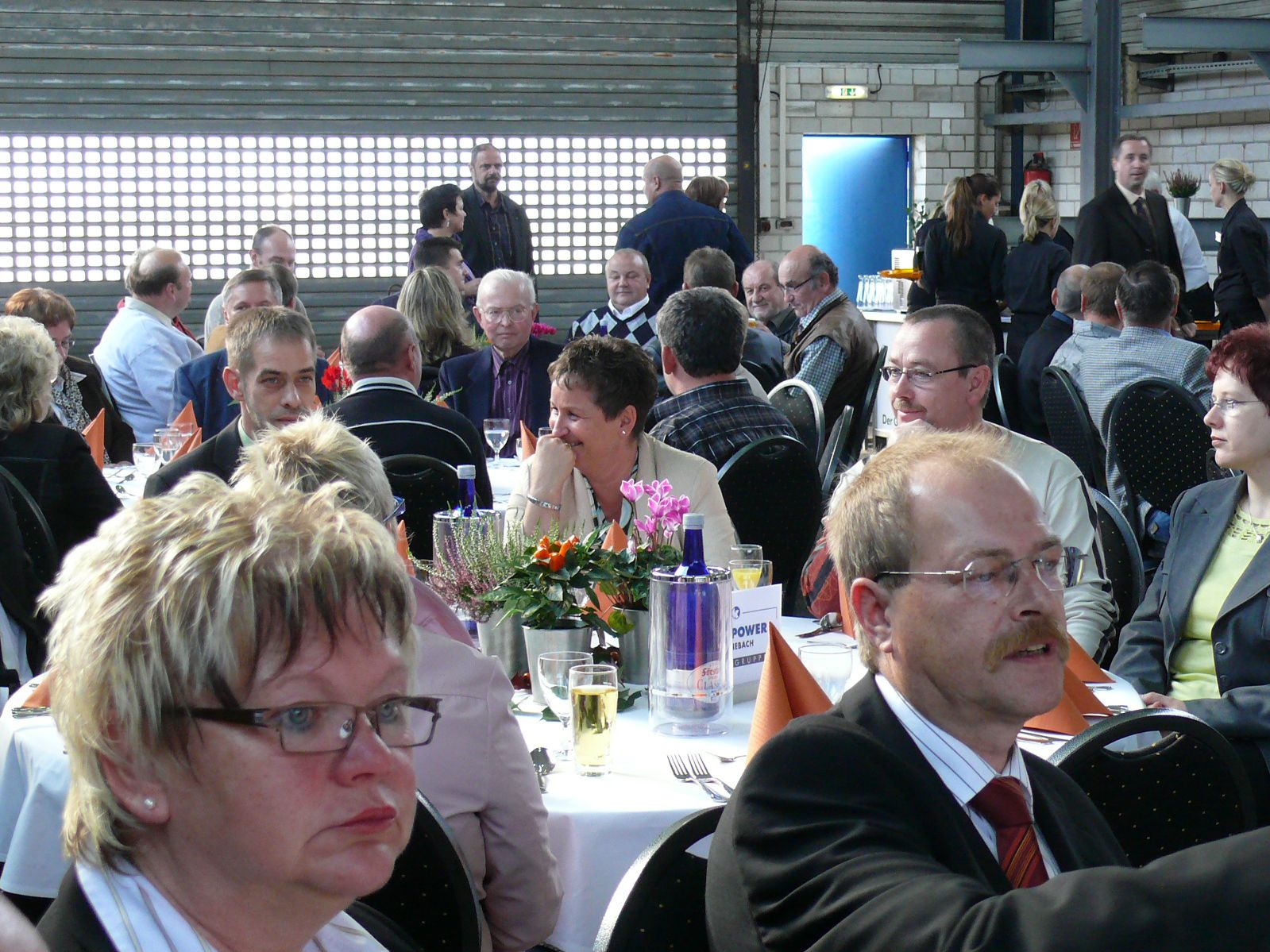
|
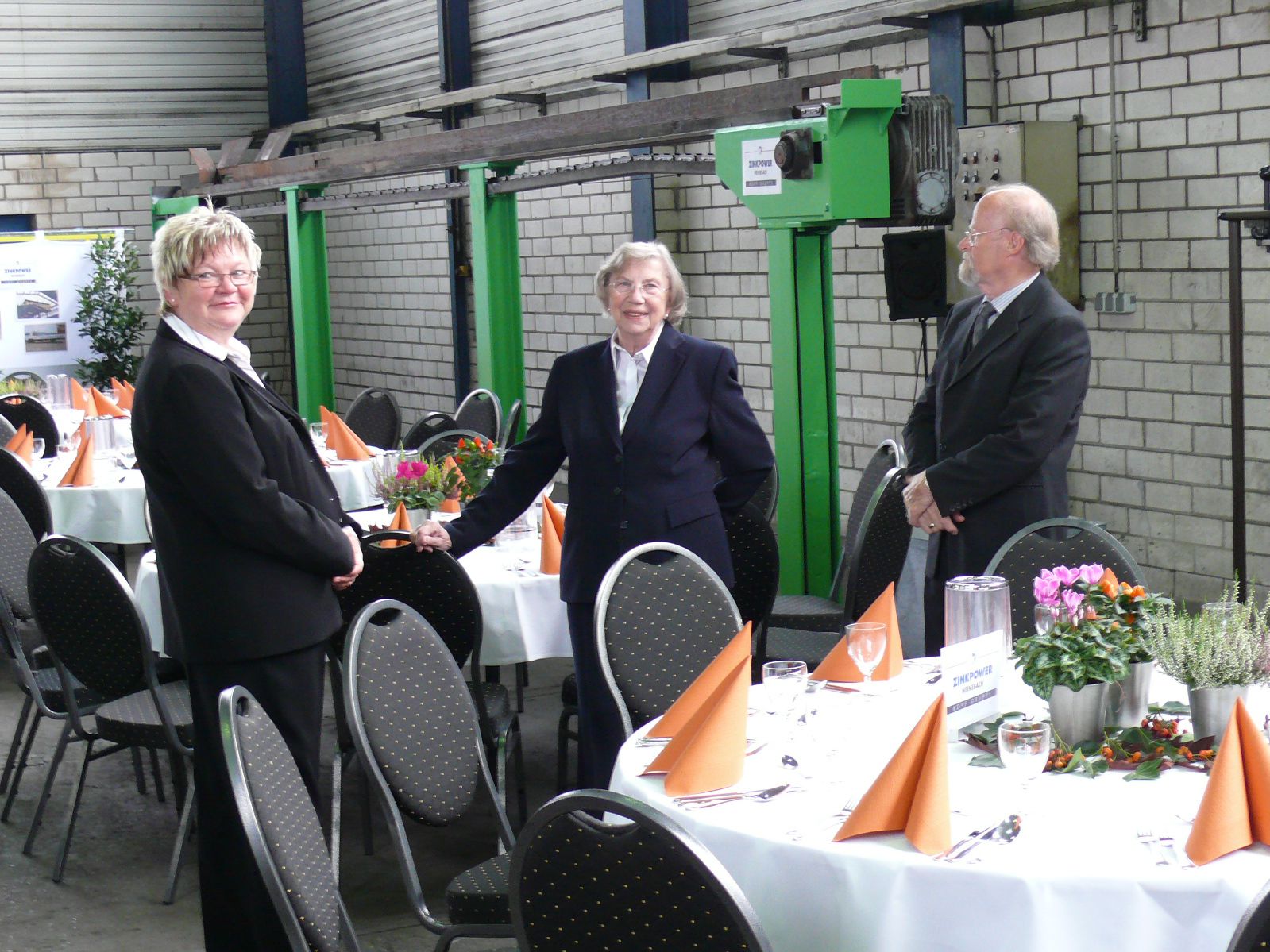
|
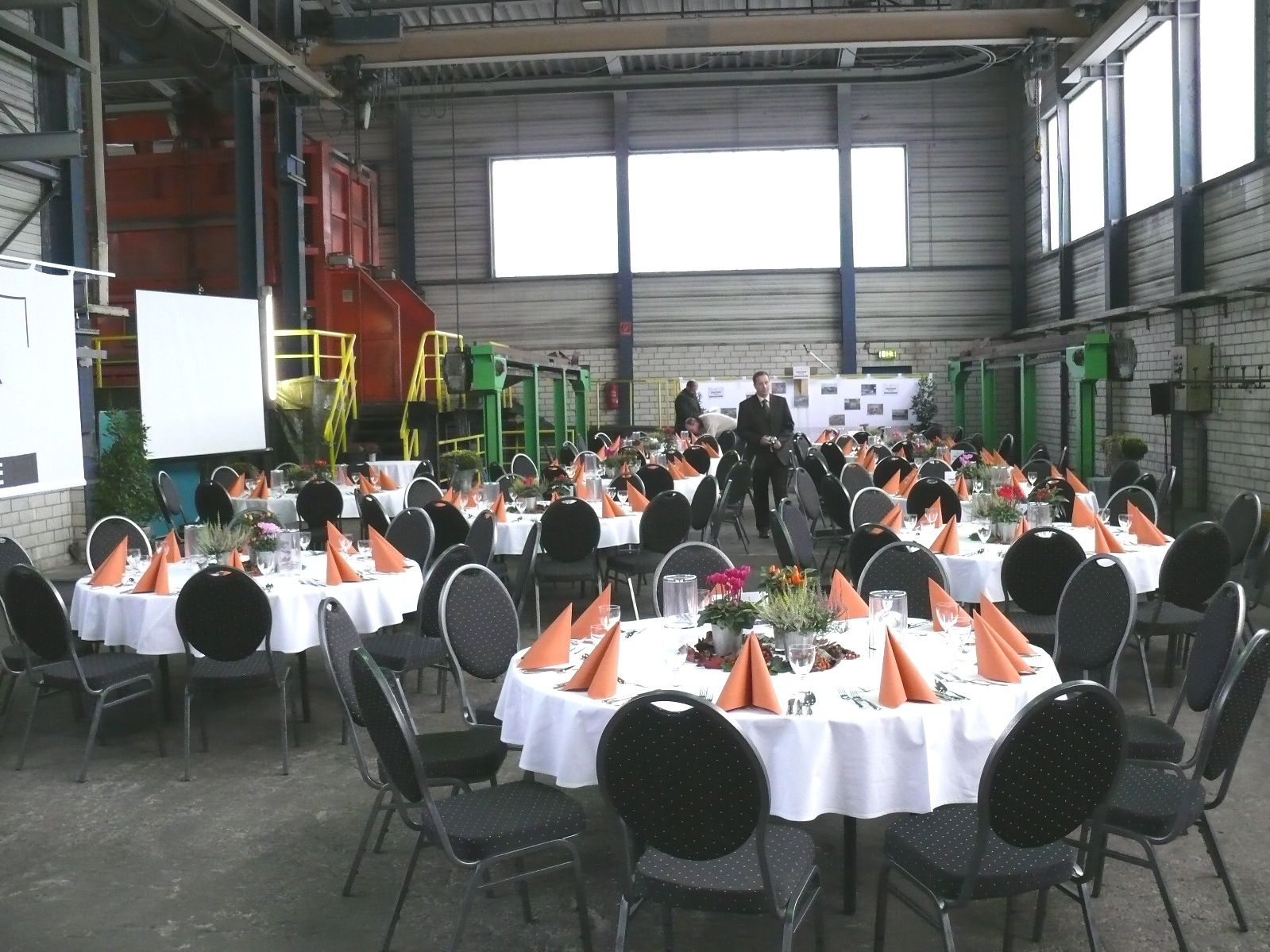
|
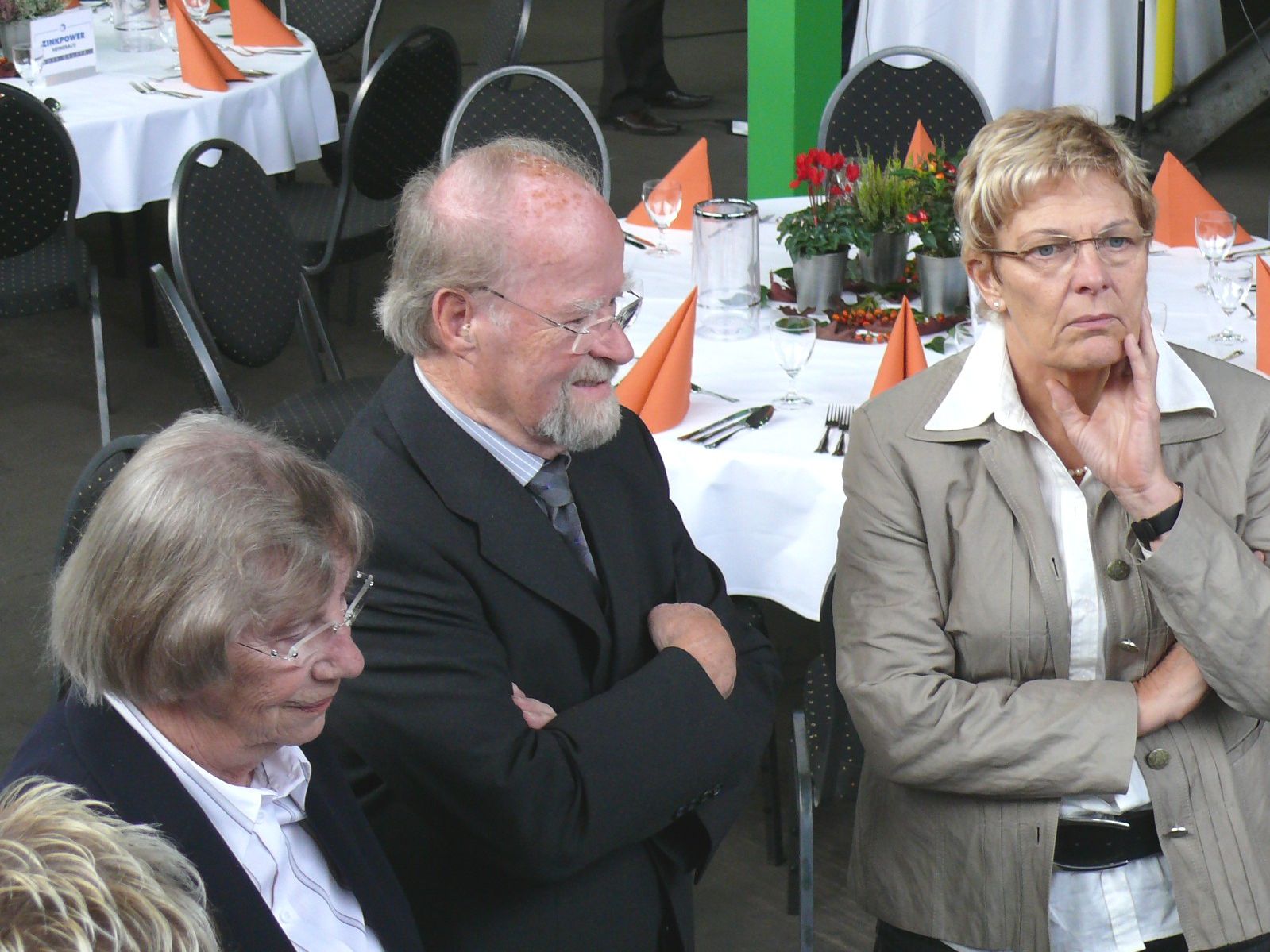
|
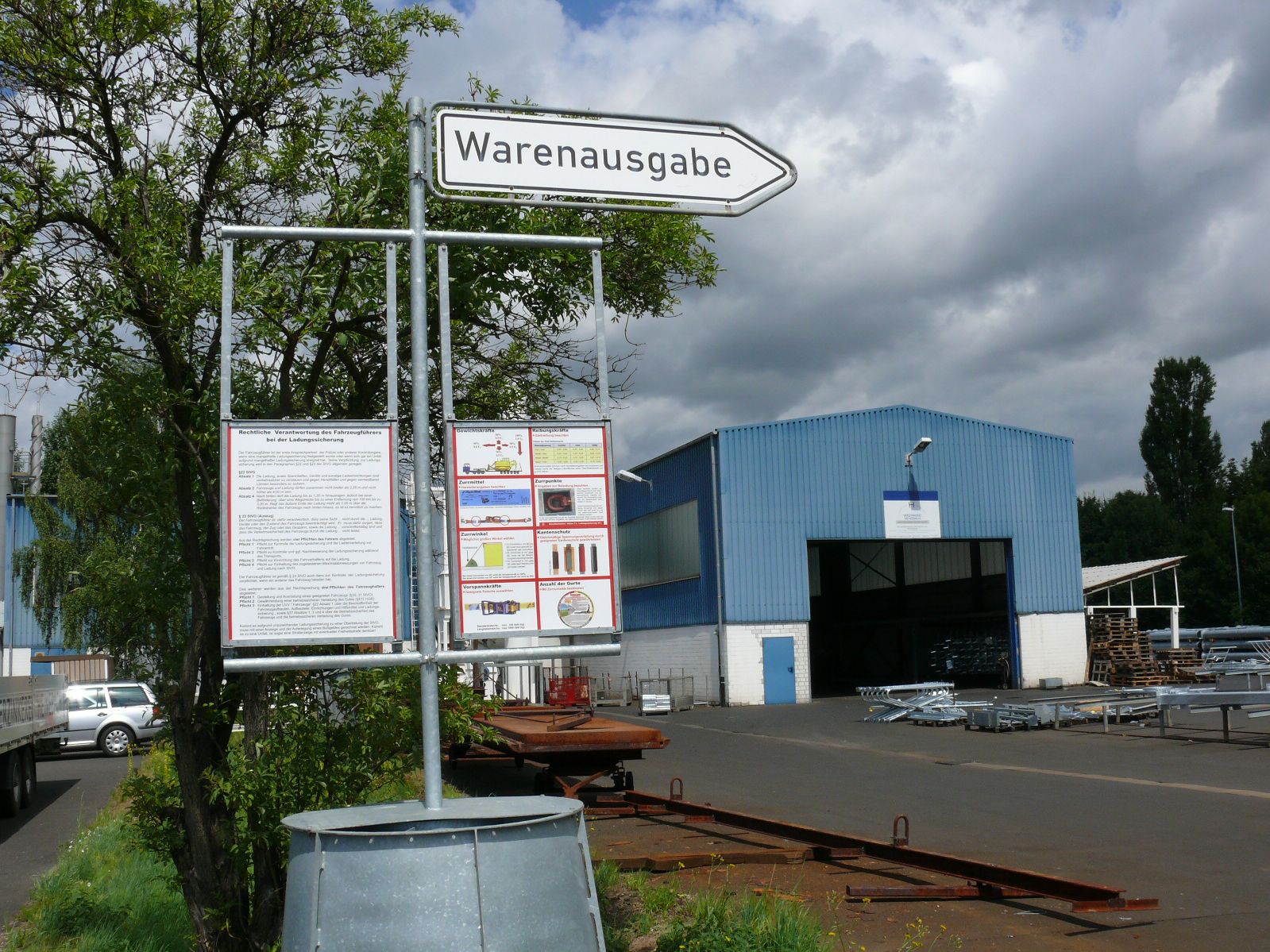
|
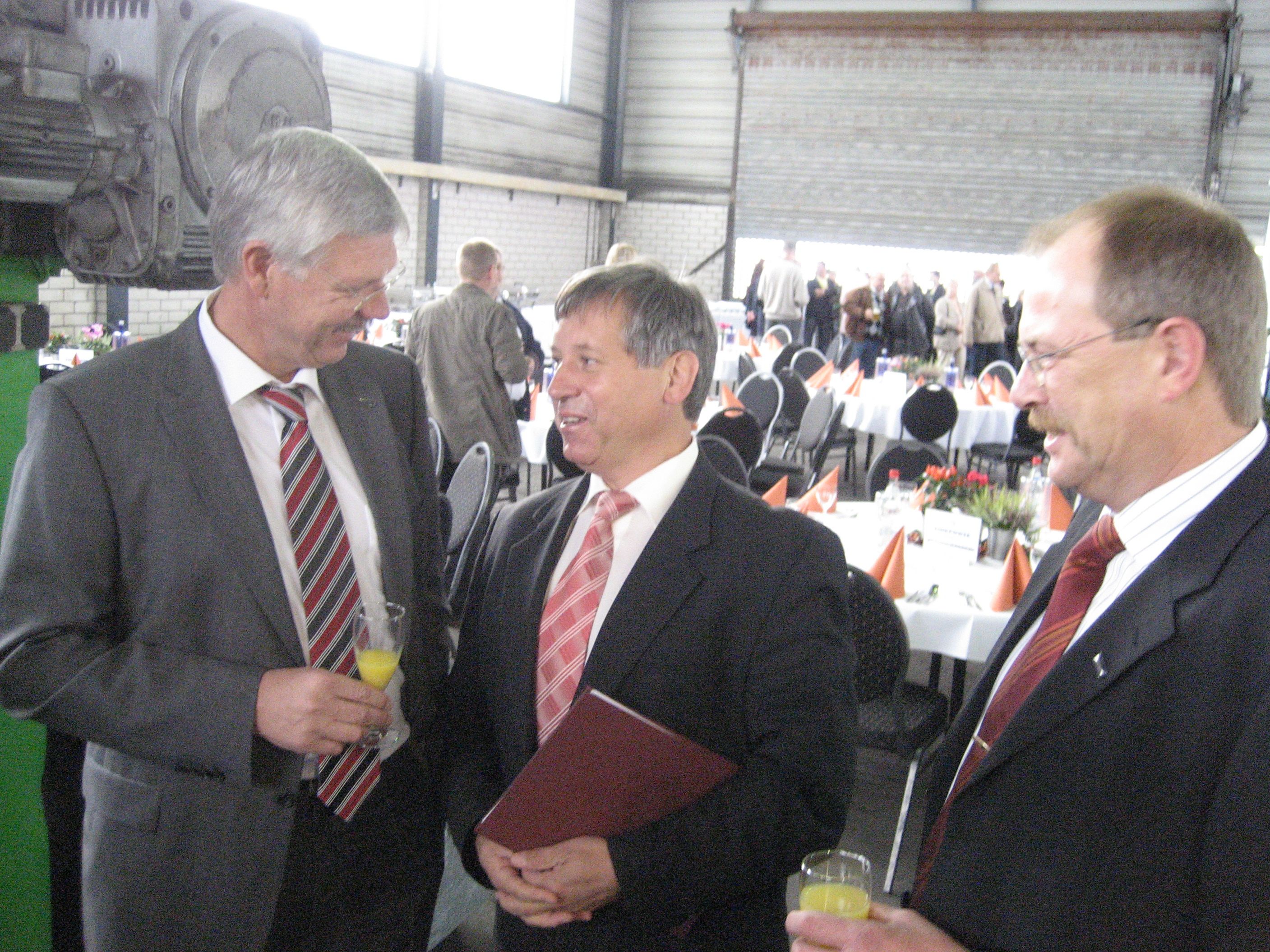
|
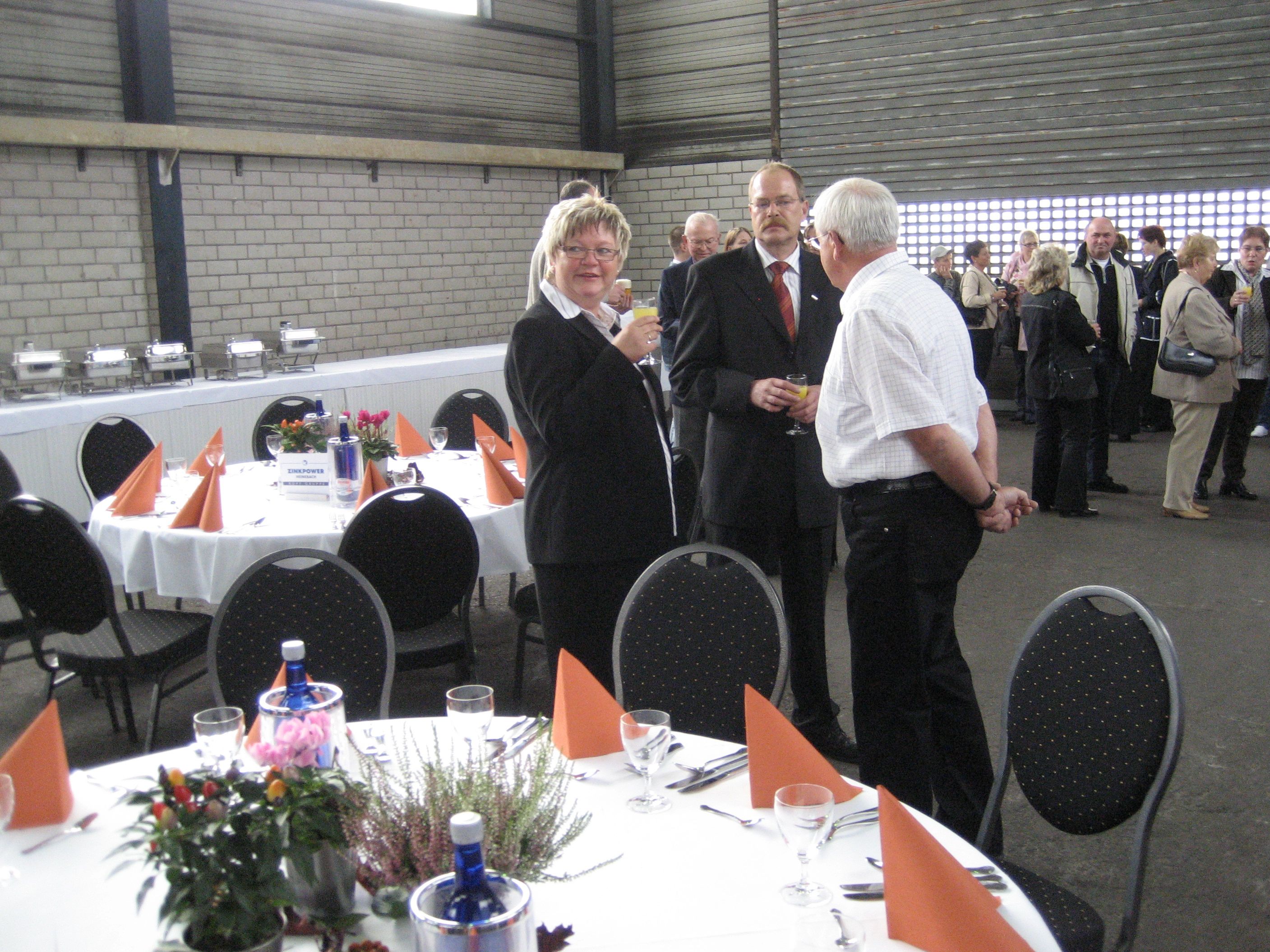
|
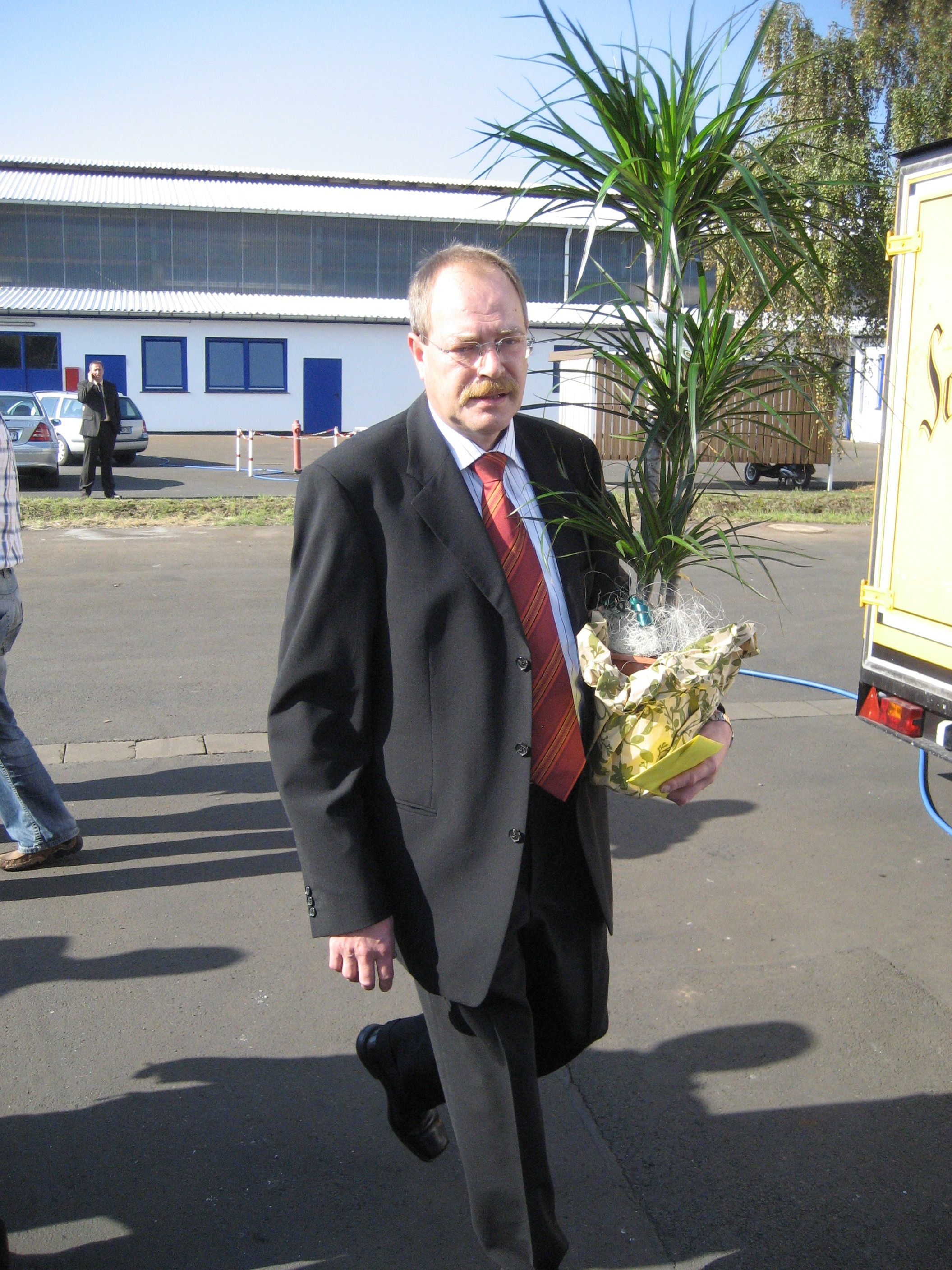
|
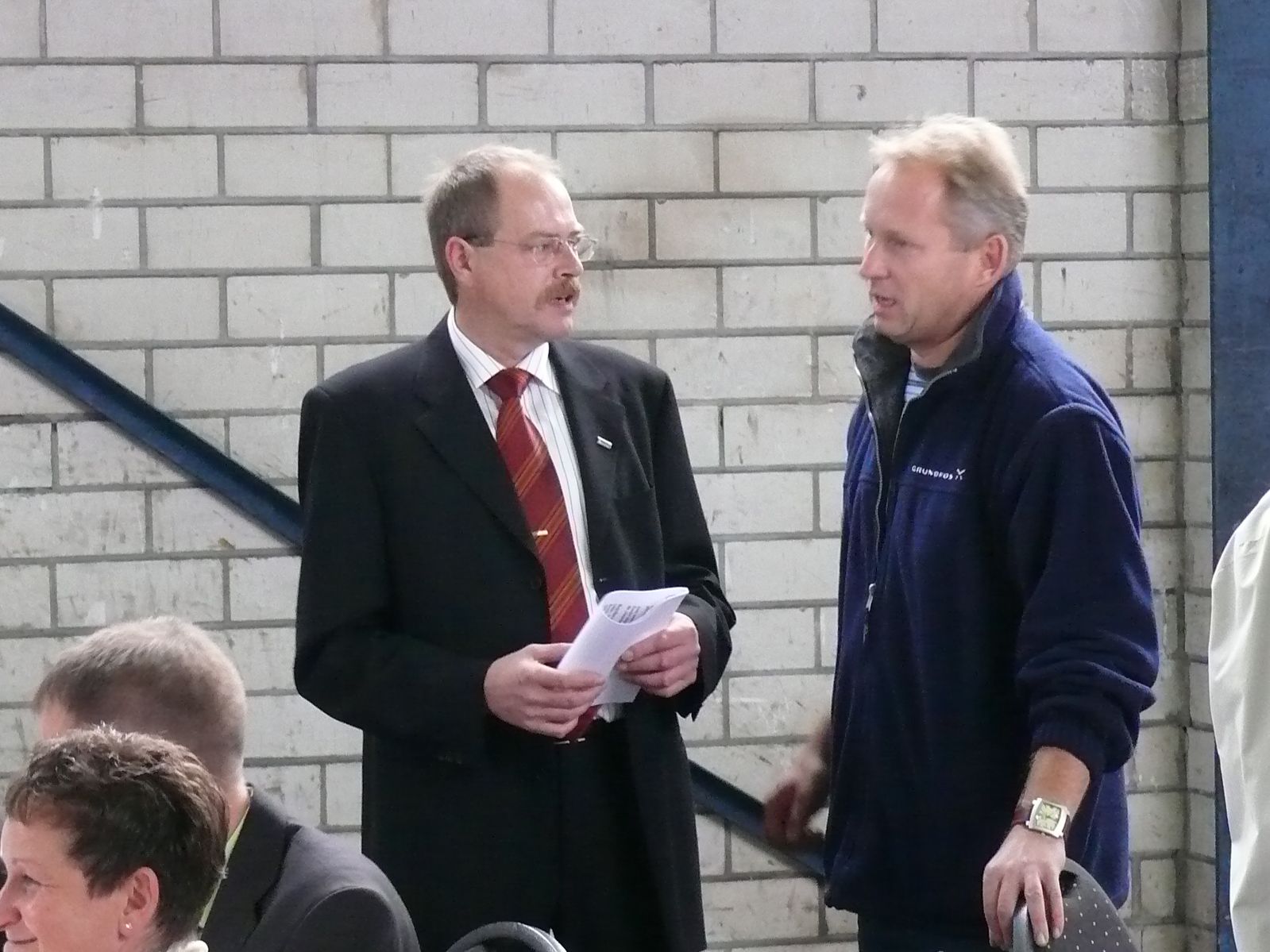
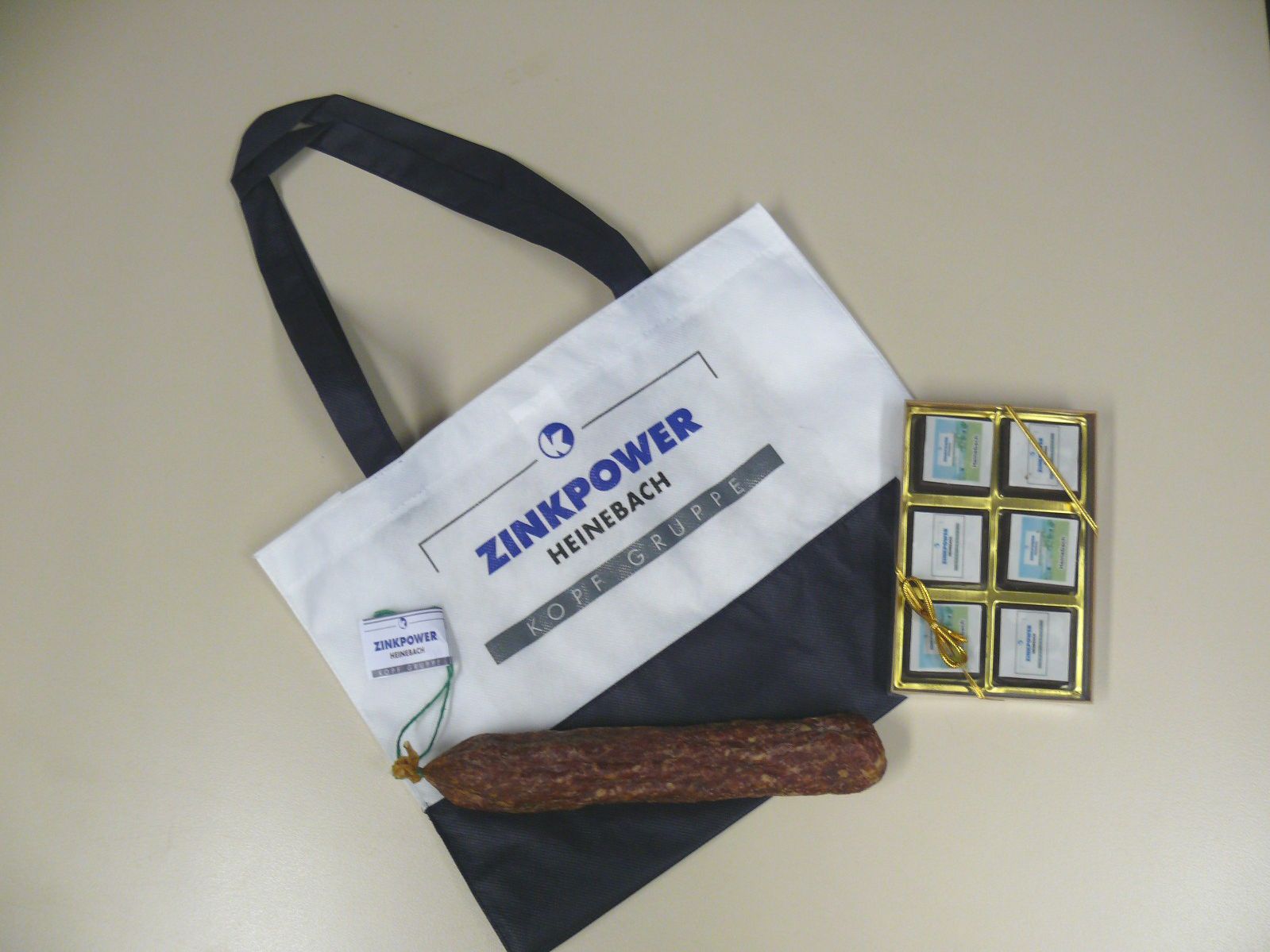
|
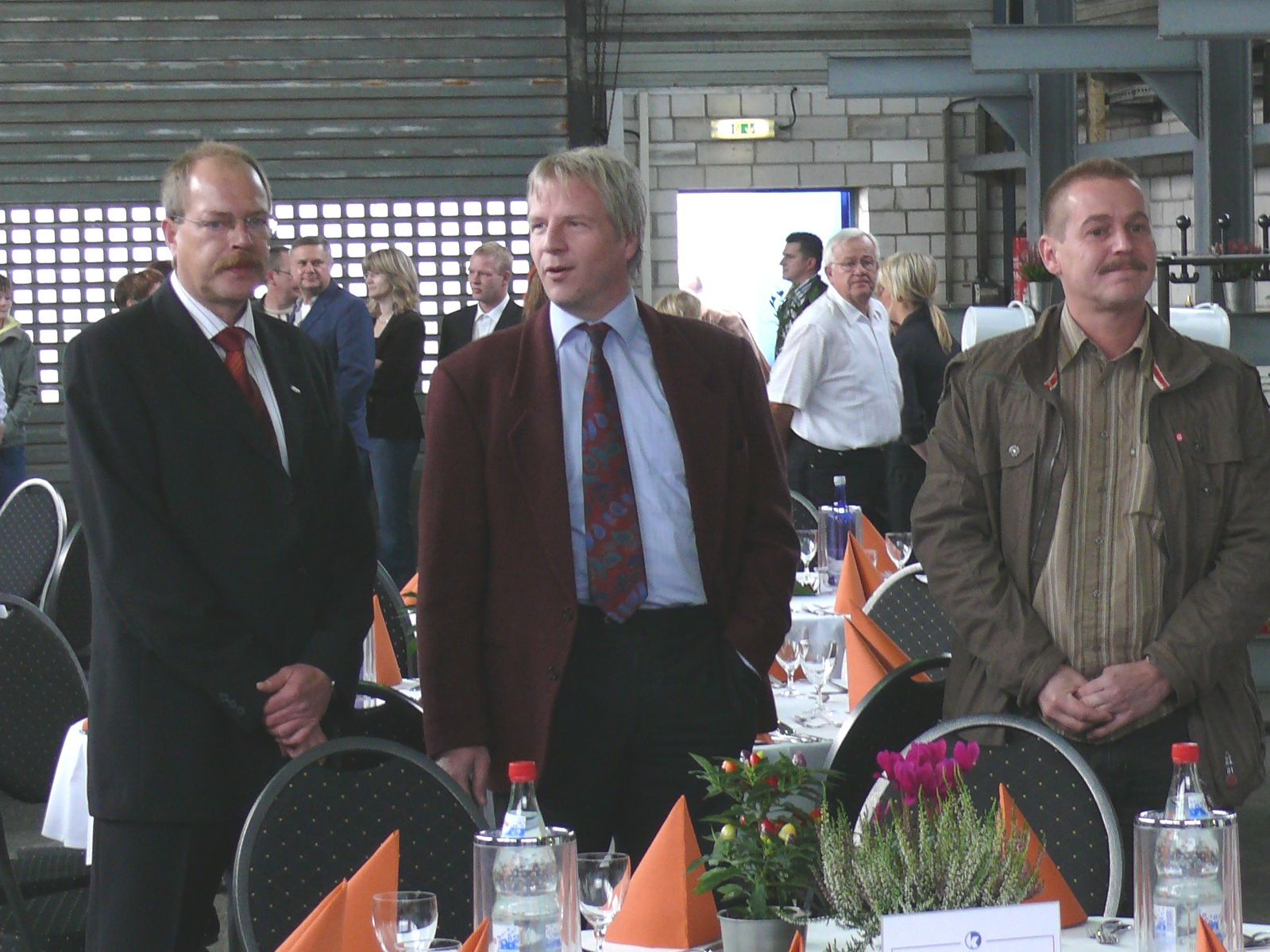
|
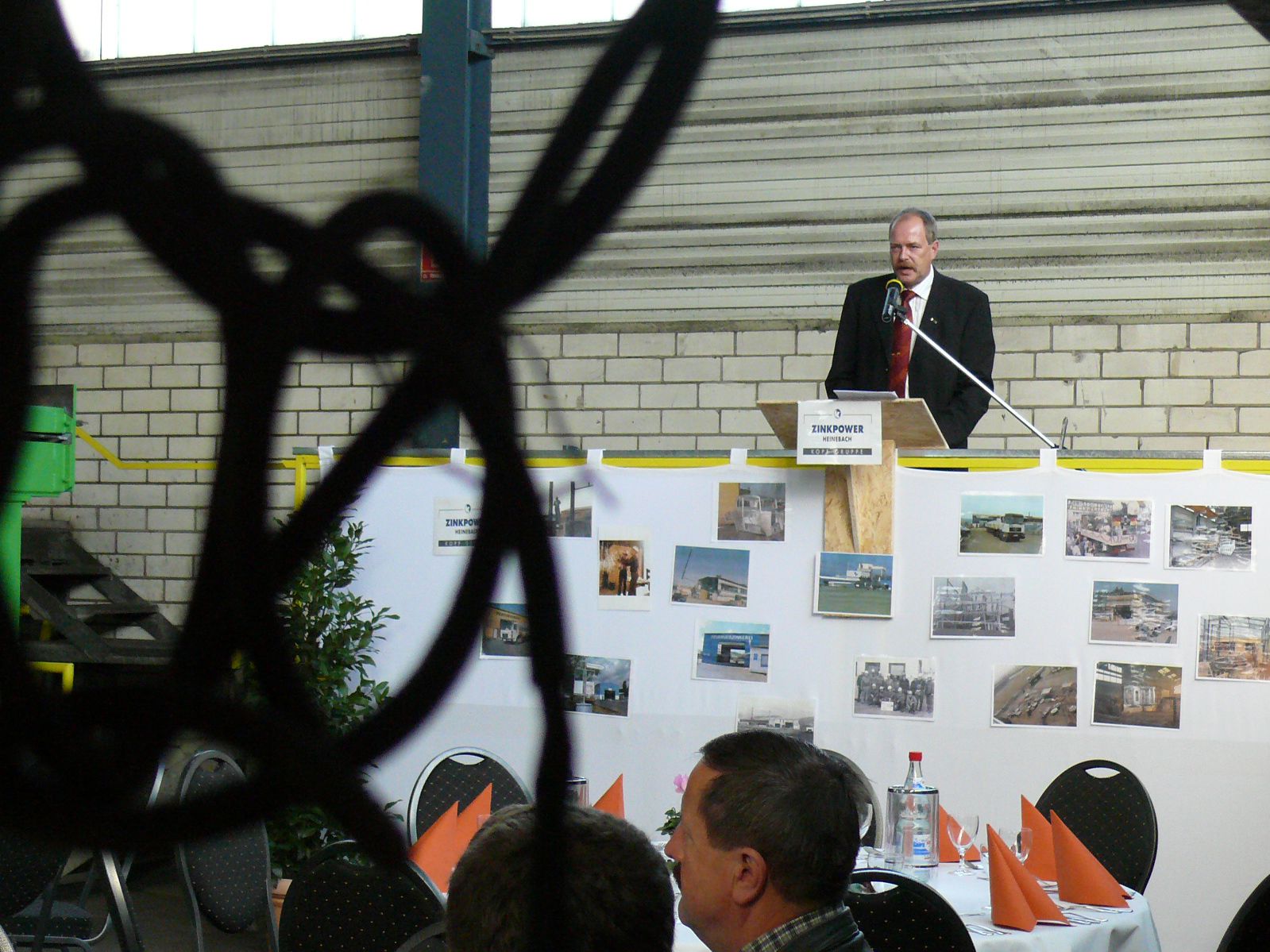
|
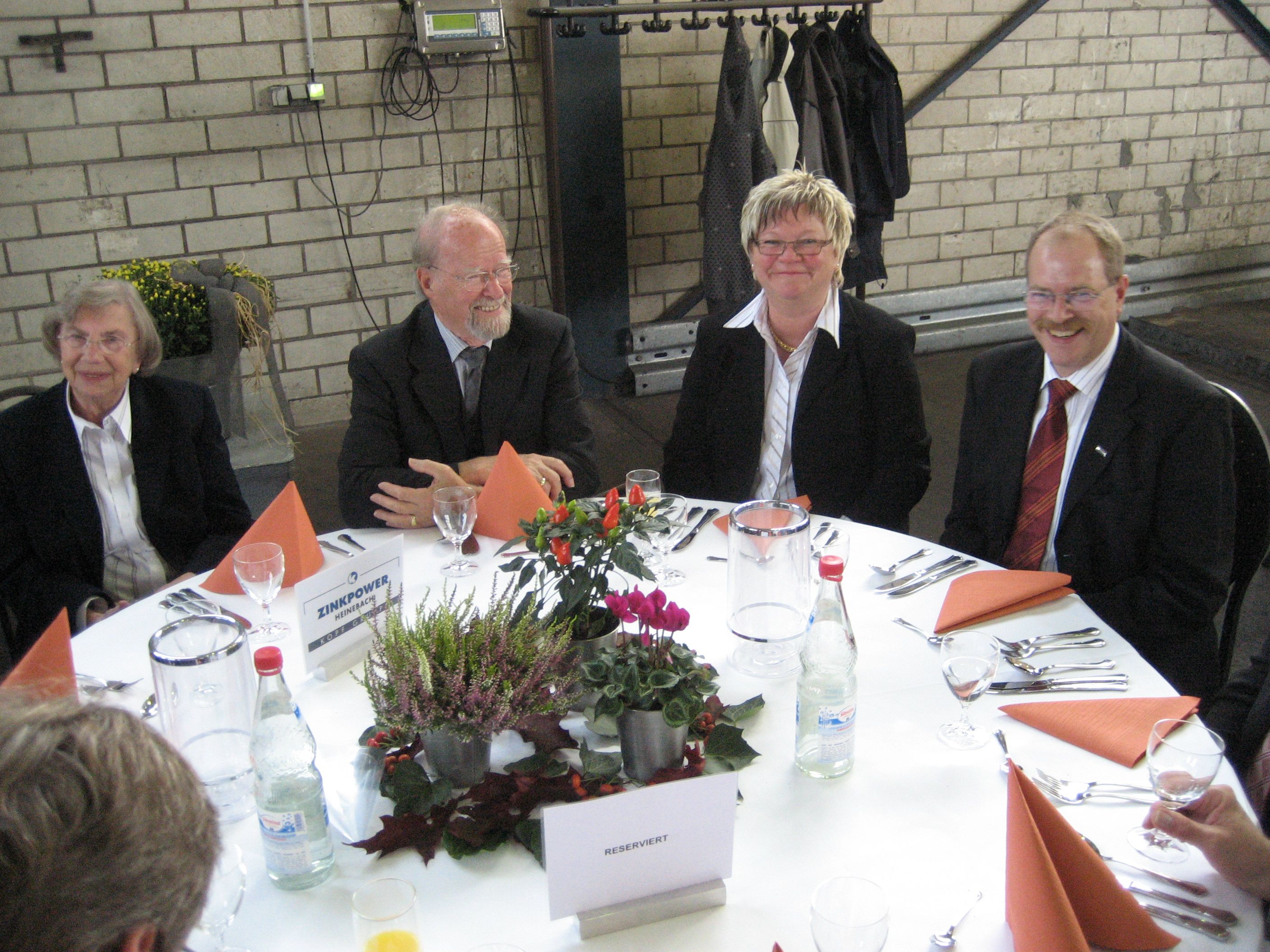
|
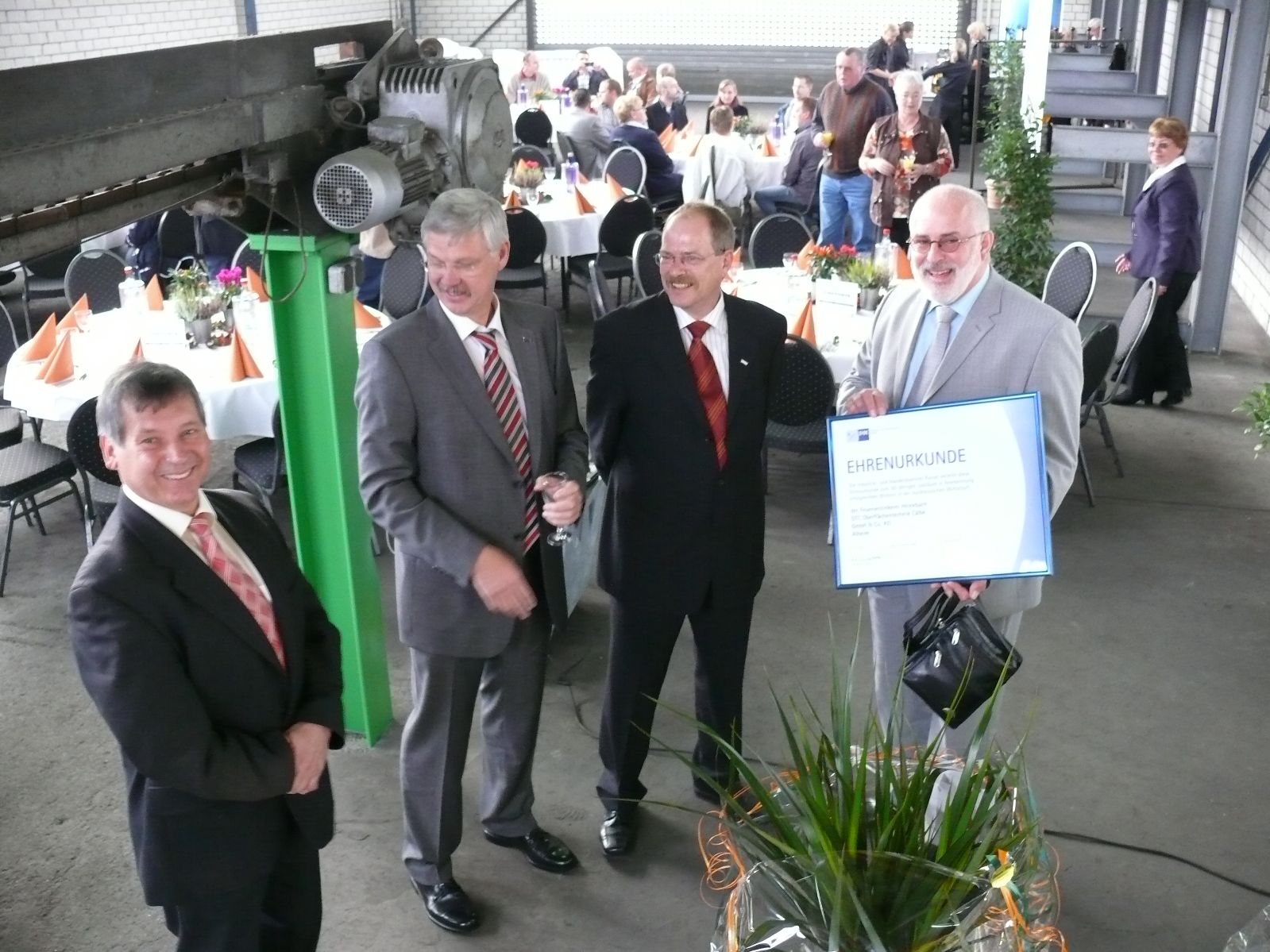
|
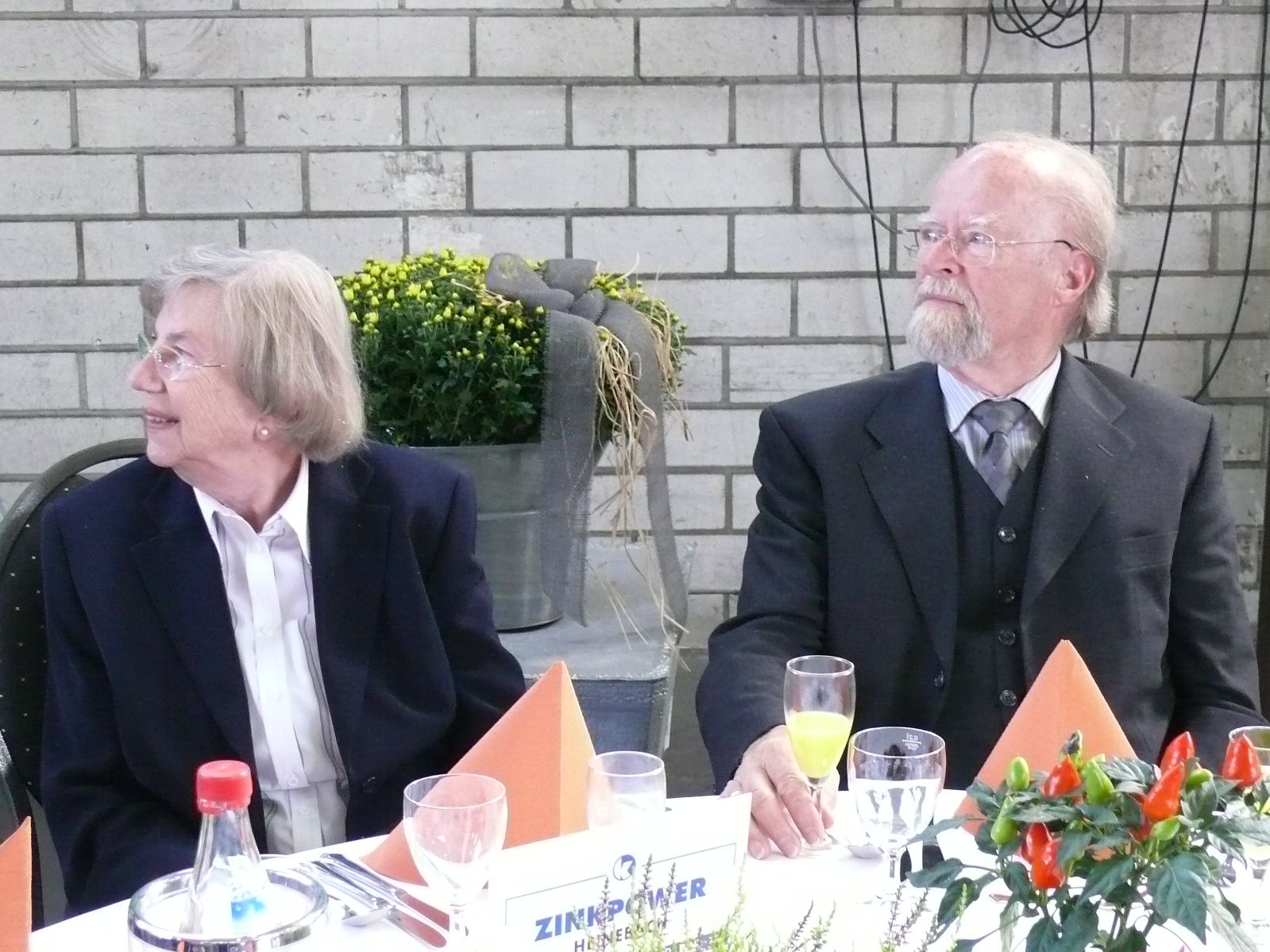
|
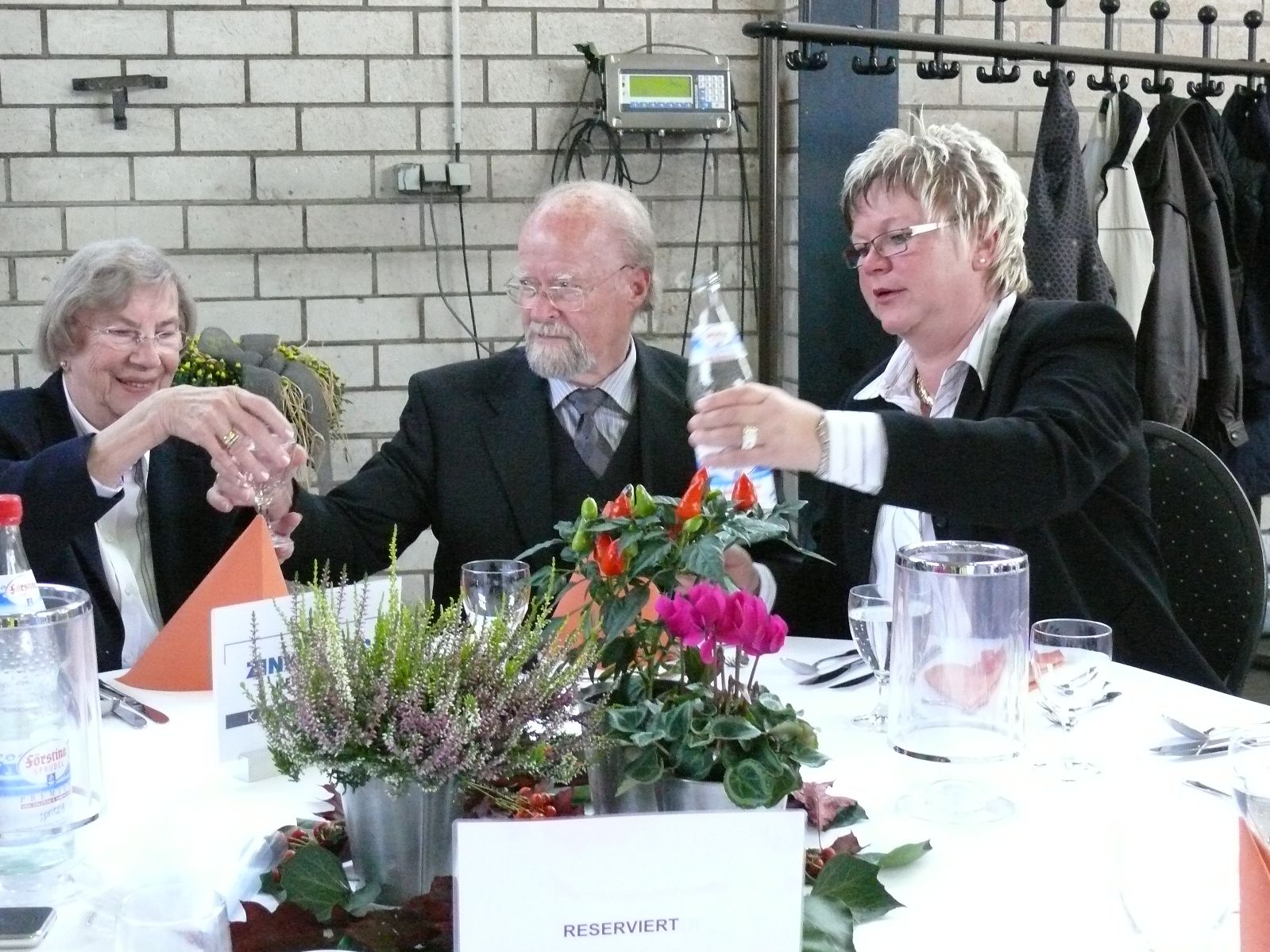
|
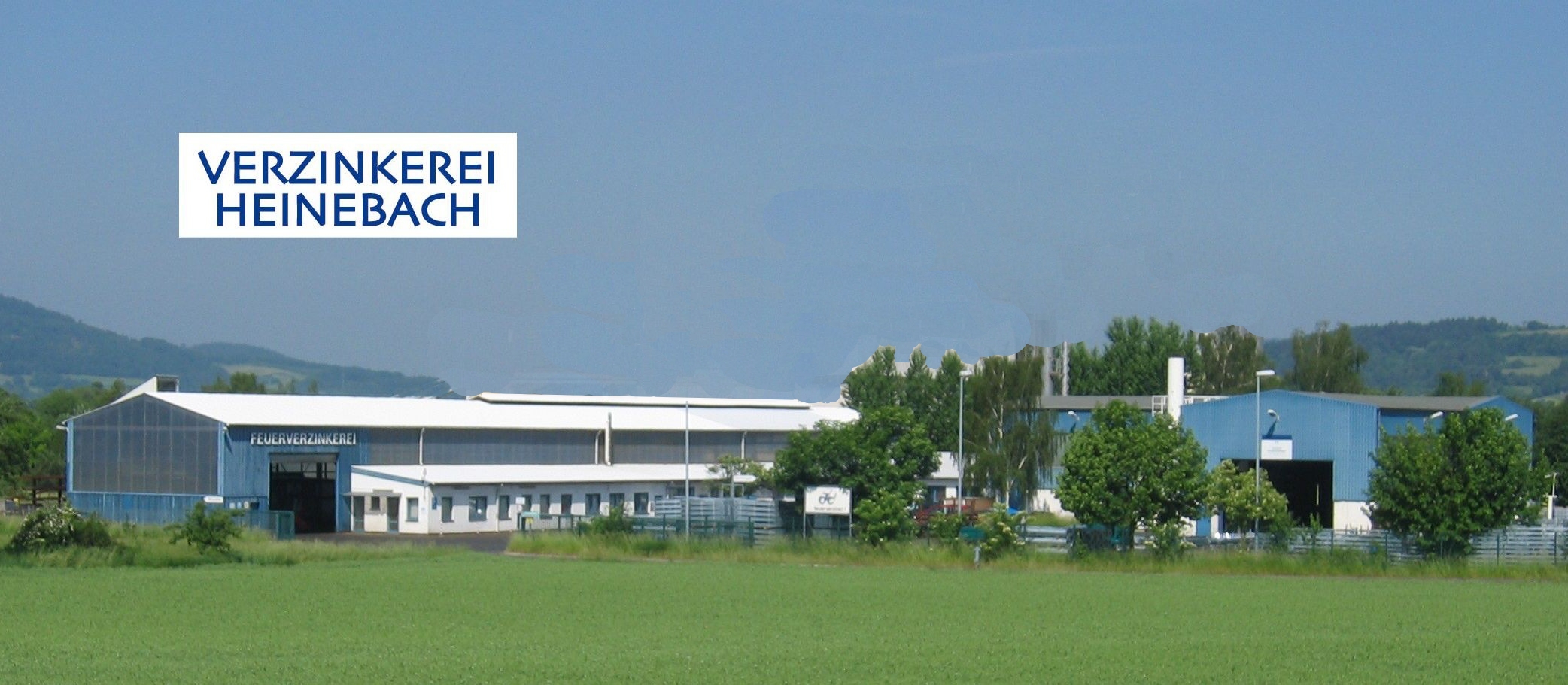 |
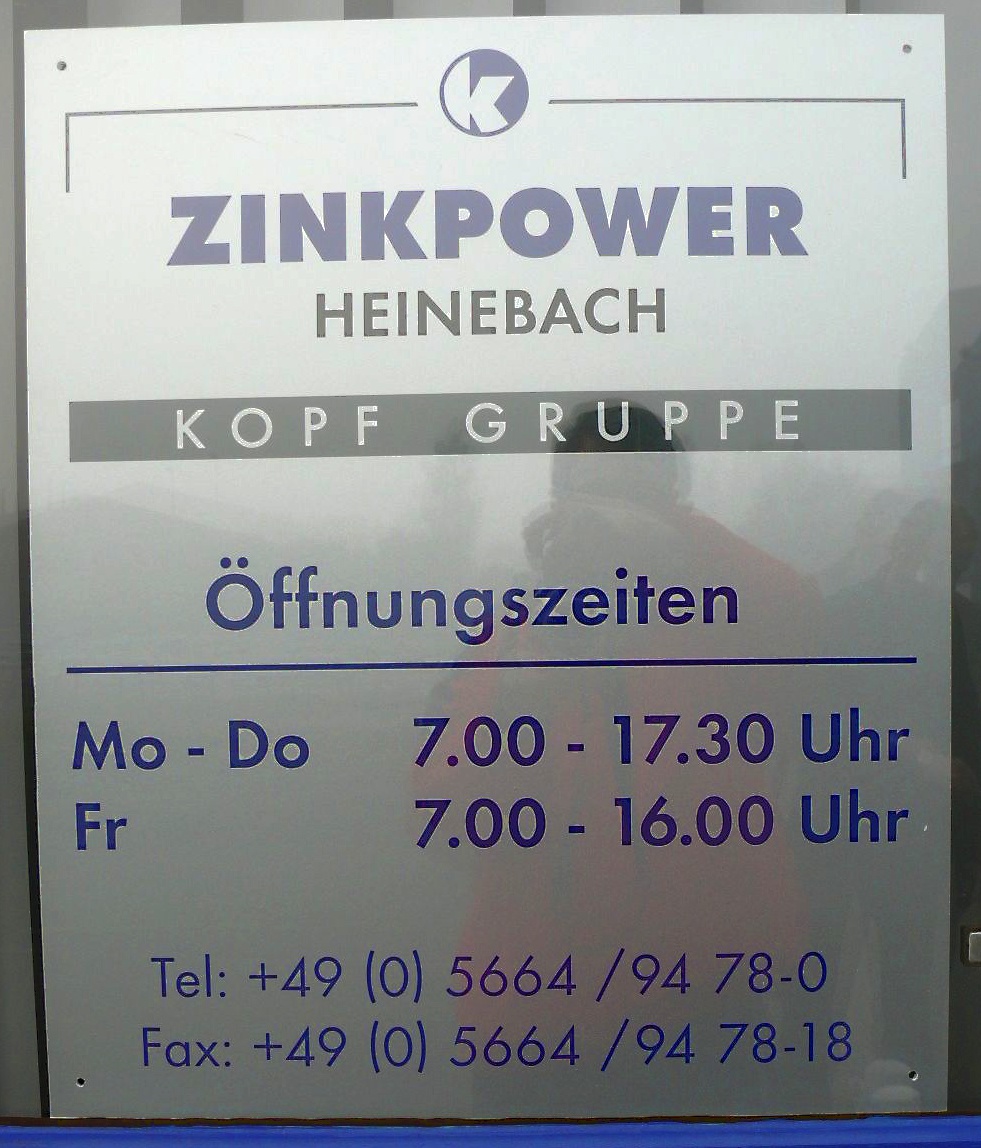
|
|
Am
01.10.2008
erfolgte die Abspaltung von OTC Calbe. Heinebach war von
da an ein eigenständiger Betrieb und firmierte unter Zinkpower
Heinebach GmbH u. Co KG.
Zum
30.09.2014
wurde der Betrieb geschlossen.
Meinhard Wittich - Spangenberg, Dezember 2018 |
|
|
|
|